Alexander NOSKOV
Deputy Director for Science, D. of Tech. Sc.,
FRC Institute of Catalysis of the Siberian Branch of RAS
e-mail: noskov@catalysis.ru
Maksim KAZAKOV
Senior Researcher, Scientific Secretary, D. of Chem. Sc.,
FRC Institute of Catalysis of the Siberian Branch of RAS
e-mail: kazakov@catalysis.ru
Total world reserves of liquid hydrocarbons are estimated at 1.7-1.8 trillion tons; the share of conventional oil in this pool does not exceed 10-12%
Unconventional hydrocarbon resources include resources located in complex geological conditions whose development requires the use of new methods and means of their exploration, production, processing and transportation.
taking into account geological, economic, social and environmental factors [1]. Table 1 shows the classification of the main types of non-traditional (hard-to-recover) oil and gas, presented in [2].
The ratio of natural gas/shale gas/coalbed methane resources is 1:1:1 and is estimated for each source at about 200 trillion cubic meters. The much greater potential of hydrocarbon raw materials in comparison with traditional oil lies in the resources of natural bitumen and oil shale.
Estimates show that in the first half of the 21st century, worldwide conventional oil production will reach a historical maximum that will be maintained for about 10 years, at which point production levels will begin to decline [3]. Unconventional hydrocarbons are attracting considerable attention as one of the most obvious sources for expanding the resource base of refineries. This is primarily due to the depletion of conventional oil reserves, on the one hand, and the growing demand for high-quality oil products, on the other. In addition, the total content of hydrocarbons in unconventional sources significantly exceeds the total reserves of conventional oils (see Table 2) [4].
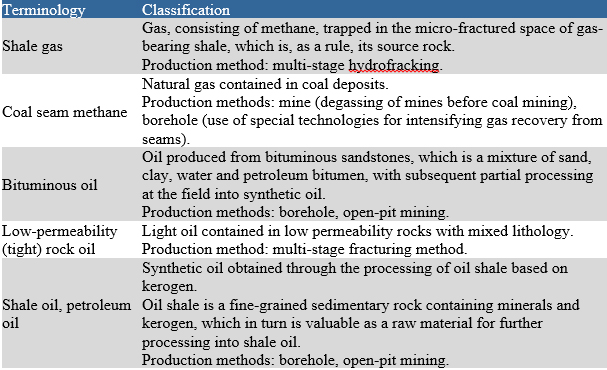
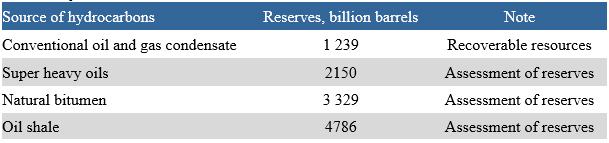
Total world reserves of hydrocarbons in the oil sector are estimated at 1.7-1.8 trillion tons, and the share of conventional oil in this pool does not exceed 10-12%. The involvement of sources of unconventional hydrocarbon raw materials in production is complicated by the relatively low hydrogen/carbon ratio in their organic component (see Fig. 1) [5].
Below are the characteristics, estimates of resources in different regions, and directions of processing of natural bitumen and oil shale.
Natural bitumen
Natural bitumen is found primarily in the form of tar sands.
The term “tar sand” is commonly used to describe sandstone impregnated with a heavy, viscous, naturally-occurring bituminous material that is substantially immobile in the field. Tar sand is a mixture of sand, water and bitumen [6, 7]. The heavy organic material has a very high viscosity in reservoir conditions and cannot be recovered from the well by conventional production methods, including oil stimulation methods [8], which are currently applied. The highest quality tar sands contain up to 18 wt.% of bitumen, whose consistency can be equivalent to that of atmospheric or vacuum oil residue.
Table 3 provides information on the reserves of natural bitumen in various regions of the world [4].

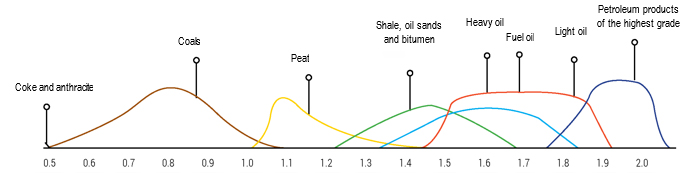
Whereas in conventional oil, hydrocarbon content reaches up to 97 wt%, only 50-60% of bitumen can consist of hydrocarbon components. The rest consists of compounds of sulfur, oxygen, nitrogen, metals
As can be seen from the presented data, the bulk of the world’s natural bitumen reserves (about 2/3) is located in Canada. In most countries, the data is clearly insufficient to make accurate estimates of natural bitumen reserves. For example, preliminary geological information indicates significant natural bitumen resources in the East Siberian platform. However, in this area, resource estimates were obtained only for the Olenek field. Detailed geological exploration aimed at natural bitumen will likely lead to a significant revision of the natural bitumen resource ratio among the regions of the world.
Compared to conventional oil, whose hydrocarbon content can reach up to 97 wt%, no more than 50-60% of natural bitumen can consist of hydrocarbon components. The rest consists of compounds containing sulfur, oxygen, nitrogen, metals. The high content of asphaltenes and resins in natural bitumen also complicates their qualified processing into marketable oil products (motor fuels, raw materials for petrochemicals).
Oil shale
Oil shale is a mineral consisting of organic (sapropelic or humus-sapropelic) and mineral (lime, clay, siliceous, etc.) parts. The content of organic matter in oil shale can range from 10-30 to 50-70 wt%, and the hydrogen content reaches 7-10 wt%. The main part (90-95%) of organic matter is a solid substance insoluble in organic solvents known as kerogen. The potential resources of oil shale in the world are enormous and are estimated at about 4.8-5 trillion barrels of shale oil (thermally processed product). Oil shale resources by region and country are shown in Table 4.
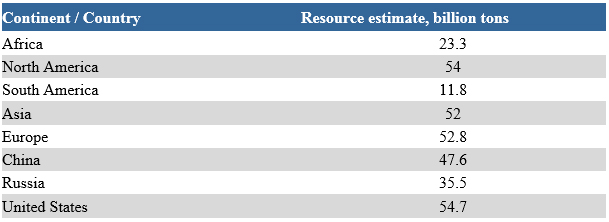
The organic basis of shale is kerogen. It is a random combination of hydrocarbon monomers. Liquid hydrocarbons can be obtained by their thermal decomposition
The accuracy of the presented data leaves much to be desired. Only the reserves of a few oil shale fields are described quite accurately (for example, the Green River field in the USA, fields in Estonia). It is worth paying attention to the relative uniformity of the distribution of carbonaceous shale resources across the regions of the world.
The main organic component of oil shale is kerogen, which is a random combination of hydrocarbon monomers. The production of liquid hydrocarbons from oil shale is possible due to the thermal decomposition of kerogen. The temperature at which active kerogen decomposition starts is nearly identical for oil shale of various origins and is about 350°C [9].
Table 5 provides information on the composition of the organic and mineral parts of oil shale from various deposits.
Oil shale is characterized by an increased content of hydrogen, which contributes to the formation of liquid and gaseous products during their heat treatment. In terms of carbon/hydrogen ratio, oil shale is closer to oil than other fossil fuels (coal, peat, bitumen).
Obtaining liquid petroleum products from natural bitumen and oil shale
During the processing of tar sands and oil shale, liquid hydrocarbon raw materials are obtained that do not occur in nature. The product obtained during processing is most often referred to as synthetic oil.
Extraction and processing of natural bitumen. The industrial extraction of natural bitumen from tar sands began in Canada in the 1960s. A small fraction (up to 20%) of Canada’s natural bitumen can be recovered by open-pit mining. For the extraction of natural bitumen, downhole methods are also actively used, based on the treatment of tar sands with a hot heat carrier or solvent.
Hot water extraction is the main commercial technology for extracting natural bitumen from open-pit tar sands. This method involves softening the bitumen by mixing it with hot water or steam, followed by the separation of sand and bitumen. Further purification of bitumen from water and solid particles is carried out at the second stage of the process by the extraction of bitumen with light hydrocarbon solvents (naphtha, kerosene, etc.). After extraction, the solvent is separated from the bitumen composition.
Sludge waste from bitumen mining contains a lot of clay and consists of about 49-50 wt.% sand, up to 1 wt.% bitumen and about 50 wt.% water.
It requires a lot of water and heat consumption
One of the main problems arising in the separation of bitumen from tar sand by hot water extraction is the need for the expensive process of tailings sludge disposal containing residues of bitumen, alkalis and other pollutants, the deposition of which occurs in settling ponds (sludge lakes) occupying vast areas. Sludge waste contains a lot of clay and consists of about 49-50 wt.% sand, up to 1 wt.% bitumen and about 50 wt.% water. In addition, these technologies are characterized by their significant consumption of water, heat and solvents.
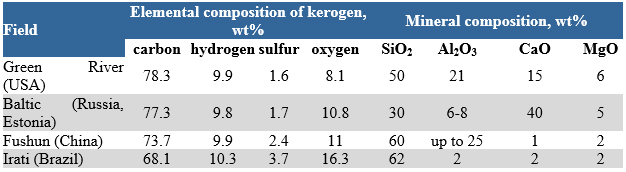
Downhole thermal methods require significantly higher energy consumption than open-pit mining methods. Downhole technologies are currently being developed without the use of steam
Downhole methods started being actively used for industrial bitumen extraction later than open-pit methods. Bitumen extraction rates for such methods vary from 10% (cold bitumen extraction with sand) to 70% (steam-assisted gravity drainage method) and potentially more than 80% for underground combustion technologies [10]. Of the thermal methods, formation steam cycling was mastered first, followed by continuous steam-assisted gravity drainage with two horizontal wells located one above the other.
Downhole thermal methods, as a rule, require much higher energy consumption to extract bitumen than open-pit mining methods. Therefore, research and development is currently underway on new downhole technologies without the use of steam. The most promising of them is the technology of underground combustion of part of the bitumen in a directed front along a horizontal well.
Using this technology [11], a bed of heavy hydrocarbon cracking catalyst is placed in the formation along the horizontal section of the production well on the path of the extracted hot bitumen. It can be placed inside the horizontal perforated section of the well, or in the formation around it. Reducing gases (Н2 or CO) can be injected into the same zone, if necessary, through a separate well located inside or next to the air injection well. Under the impact of high temperatures in the presence of reducing gases in the catalyst bed, heavy hydrocarbons are decomposed, bitumens are demetallized and desulfurized, and their viscosity is decreased. Since the catalyst is distributed along the entire well, and the catalyst sections are gradually, in parts, opened to the processed bitumens as the combustion front moves, a corresponding zone of fresh high-activity catalyst is maintained for each section.
Bitumens separated from tar sands have a very high viscosity and are unsuitable for transportation by pipeline. In order to meet the density and viscosity requirements of pipeline pumping, two approaches are used. The first approach is based on the dilution of bitumen with lighter hydrocarbons (light oil, naphtha, gas condensate). The second approach involves the partial processing of bitumen into lighter synthetic oil near the production areas and transportation of the resulting synthetic oil to refineries without dilution.
The following main approaches are used to process bitumen into synthetic oil:
- Carbon removal: visbreaking, steam cracking, coking. Carbon removal processes are quite attractive because they operate at low pressure and do not require expensive catalysts. When processing bitumen into synthetic oils, this method is used in most cases.
- Hydrogen addition: catalytic hydroconversion (hydrotreatment, hydrocracking), hydrovisbreaking, and donor-solvent processes. Bitumen hydrotreatment processes remove sulfur, nitrogen, metals and thus prepare it for further processing by other processes. Hydrocracking provides lighter distillates (kerosene, diesel fractions) and low-sulfur residues.
Shale often contains a number of valuable components (molybdenum, vanadium, uranium, etc.) in almost commercial quantities. For example, the uranium content at the Ran Stad field reaches 1 million tons.
The process of converting bitumen into synthetic oil is carried out in two main stages. First, the primary processing of bitumen is carried out to increase the hydrogen/carbon ratio through the: a) removal of carbon or b) addition of hydrogen. Then, the resulting products of the primary conversion are separated and processed by hydrotreatment to remove sulfur and nitrogen. The resulting synthetic oil can then be transported to refineries for processing into various liquid fuels such as gasoline, kerosene and diesel fuel. Further processing of the synthetic oil should reflect the fact that compositions of synthetic oils differ from those of natural oil of the same density. Firstly, most of them have no vacuum residue, which is unusual for refineries implementing a process with vacuum residue coking. In addition, synthetic oils have little gasoline, a lot of gasoils, including heavy vacuum gasoils, and a high content of aromatic compounds. Therefore, the diesel fuels obtained from such raw materials have low cetane numbers. In this regard, the processing of synthetic oils requires increased capacities for the hydrocracking of vacuum gasoils. Since synthetic oils are often the product of thermal cracking, they are characterized by a high olefinicity, which, in the absence of hydrotreatment and their saturation, causes their instability during storage and transportation. Most often, when refining at existing refineries, synthetic oil is blended with natural oils to approximate conventional formulations.
Coking processes are the main processes for upgrading bitumens, which are used to convert them into distillable products. During the coking process, bitumen is converted into distillable fractions, coke and light gases. The resulting distillates are hydrotreated to obtain low-sulfur synthetic oil. In general, the composition of the products obtained as a result of coking is close to that of bitumen and the heavy oil residues of conventional oil.
An increase in the hydrogen/carbon ratio is also ensured by the use of hydrocracking processes [12]. Hydrocracking processes can be viewed as an alternative to coking processes. The total liquid yield in bitumen hydrocracking is much higher than in coking. It also removes significant amounts of sulfur and nitrogen. However, wide use of these processes is currently constrained by the need for large capacities for the production of hydrogen.
Oil shale processing. Modern real-world technologies for the thermal processing of oil shale are based on pyrolysis with the formation of gaseous, solid (coke) and liquid (naphtha, distillate fuel) products [5]. During pyrolysis, macromolecules of kerogen are depolymerized. Pyrolysis processes are based on heating the initial oil shale to a certain temperature in the absence of oxygen.

Source: medium.com
The share of conventional gas in total resources of gaseous hydrocarbons does not exceed 1/3. This does not include methane in the form of gas hydrates, which further reduces the proportion of conventional gas
Along with traditional thermal processing, a number of alternative methods of oil shale processing are being developed.
Among them, we could note the process of hydrocracking in a fluidized bed of oil shale and tar sands. In this case, synthetic oil from tar sands, oil shale, natural bitumen is formed due to hydrocracking and hydrogenation in a fluidized feed stream, in which the required temperature and pressure conditions are created by a stream of hot hydrogen under pressure. Carrying out the process in a hydrogen environment provides a higher yield of the target products, as well as their higher quality [13].
In the 1950s-80s, several attempts were made to develop technologies for the underground processing of oil shale. Interest in methods for the underground processing of oil shale is predicated on a number of considerations: there is no need for shale mining or the construction of surface units for shale semi-coking, which takes a long time and entails significant capital costs. However, all work on these projects was stopped due to the low profitability and certain disadvantages of the proposed technologies. Currently, the underground processing of oil shale is not being carried out and this direction can be viewed as unpromising.
The oil shale of some fields contains a number of accompanying components (for example, molybdenum, vanadium, uranium, etc.) in quantities close to commercial ones. For example, the content of U3O8 in uranium-containing oil shale from the Ran Stad field (Sweden) is estimated at 1 million tons. If we take into account that the formation of shale ash residues from the combustion of shale in some cases reaches tens of millions of tons per year, then favorable conditions are created for the extraction of some mineral components. Shale ash obtained after pyrolysis can also find use in the construction industry for cement production. Thus, the presence of accompanying minerals and rare elements could significantly change the prospects for the industrial development of shale fields. Provided that oil shale and the other minerals occurring together with them are used in an integrated manner, it may be economically feasible to process shale with a reduced calorific value.
The widespread use of oil shale has been postponed to a more distant future due to the high cost of its processing and the associated serious environmental problems.
Conclusion
The Earth’s resources of unconventional hydrocarbon raw materials significantly exceed those of the analogous ones both in natural gas and in oil raw materials. The share of conventional natural gas in the total resources of gaseous hydrocarbons does not exceed 1/3. These estimates do not include methane reserves in the form of gas hydrates, which would further reduce the share of conventional natural gas. In the oil sector, the share of conventional oil in the world’s resources of oil-oriented raw materials is even lower and does not exceed 10-12%.
To involve unconventional resources of gaseous hydrocarbons (shale gas, coalbed methane) in production it is necessary, first and foremost, to solve the problems of their extraction. Given the availability of efficient extraction technologies, the further use of these gaseous hydrocarbon raw materials doesn’t generally cause any technological issues. Much greater difficulties arise when oil-oriented unconventional resources (natural bitumen, oil shale) are involved in industrial use. In this case, it is necessary to solve the technical problems of both the extraction of this raw material and the processing of the extracted raw material into suitable liquid hydrocarbons (synthetic oil). Only after these steps is it possible to carry out highly-qualified processing of the obtained synthetic products at existing oil refineries. Currently, the mine cost of bituminous oil is $20-40 per barrel. The estimated cost of producing synthetic oil from oil shale is much higher. In current market conditions, unconventional oil-oriented resources can only be estimated as significant for the world economy in the future.
The Russian oil industry may already face a decline in oil production in the foreseeable future due to the depletion of its proven reserves and a lag in the growth of oil reserves stemming from geological exploration. At the same time, Russian oil and gas fields are characterized by a great distance from the consumer and severe natural and climatic conditions, which significantly increases the cost of extraction and increases transportation costs. One of the options for solving the problem of reducing oil production in Russia may be the organization of hydrocarbon production from unconventional sources. In all probability, traditional technologies of bitumen extraction with hot water will be inapplicable for Russian tar sands fields due to their physicochemical characteristics. The most promising for Russia will likely be the use of pyrolysis or hydrogenation processing without the preliminary separation of bitumen from tar sands. Downhole methods for extracting bitumen from tar sands using intensive physicochemical methods, including catalysis in reservoirs, may also be in demand. The widespread use of oil shale has likely been postponed to a more distant future due to the high cost of its processing and the associated serious environmental problems.
The creation of a technological platform in Russia to expand the use of unconventional hydrocarbon resources is possible through the integration of large companies (primarily oil companies) and scientific/technical organizations. It is necessary to create test sites for the development of new technologies for the extraction of unconventional hydrocarbon raw materials and their qualified processing into motor fuels, hydrogen and raw materials for petrochemicals. Unconventional hydrocarbon raw materials could emerge as one of the most important sources of hydrogen energy in the future.
This article was prepared on the basis of the results of a study carried out with the financial support of Russia, represented by the Ministry of Science and Higher Education within the framework of the scientific project “Social and economic development of Asian Russia based on the synergy of transport accessibility, systemic knowledge about natural resource potential, the expanding space of interregional interactions,” Agreement No. 075-15-2020-804 dated 02.10.2020 (grant No. 13.1902.21.0016).