Valentin PARMON
President of SB RAS, Academician, Doctor of Chemical Sciences
e-mail: secretary@sb-ras.ru
Yuri ARISTOVICH
R&D Director, R&D Centre Gasconsulting
e-mail: aristovichyv@gmail.com
Aleksey BRESHEV
Project Director of STC “Gazconsulting”, Ph.D. D., associate professor
e-mail: breshev@gmail.com
Artem VLASOV
Program Manager
for Technological Development of Gas Projects, R&D Centre Gasconsulting
e-mail: vlasov.ai@gazpromneft-ntc.ru
Grach OGANESYAN
Specialist of REC Gazpromneft-Polytech
e-mail: gra4oganesyan@gmail.com
Alexandra SAITOVA
Deputy director
of REC Gazpromneft-Polytech, Candidate of chemical sciences
e-mail: gorshkovaaa@minenergo.gov.ru
Regardless whether there is or there is no warming – but one has to do something
While scientists of all ranks, nationalities and areas of scientific interests argue hotly about the presence or absence of global warming on our planet and the possible magnitudes of its manifestations, it, this very warming, has come. No, not in nature. The team of authors does not at all intend to take one of the parties in this dispute within the framework of this article. Global warming has come in the sphere of world politics. But not in the sense of improving relations between countries – the situation is different here – but in the sense of universal recognition of significant climate change and the implementation of global measures aimed at a large-scale fight against the designated culprits of this phenomenon.
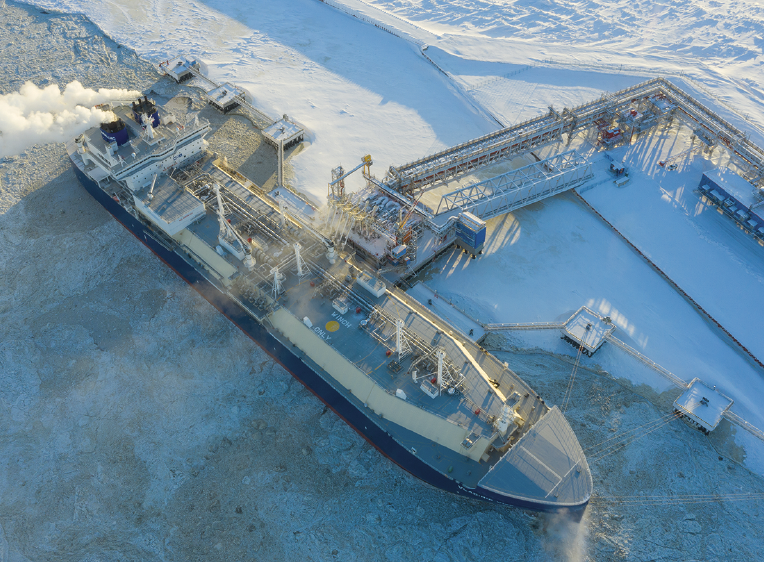
Source: KadnikovValerii / Depositphotos.com
There is no objective data that would allow one to build at least some adequate models and draw scientifically substantiated conclusions. Obviously, this does not in any way prevent the implementation of ever larger and more efficient levers driving the flywheels, springs, and somewhere the millstones of the reorganisation of world industrial production. Decarbonisation, hydrogen energy, renewable sources. These words and their combinations are not about the future – for the world industry, they already denote quite countable fines, duties, preferences and new laws of the efficiency of product production, the development of old and the formation of new markets.
We will try to find reasonable ways of possible actions for the Russian hydrocarbon production and processing industry in the already changed and rapidly transforming conditions of the action of more and more new factors.
The main trends in hydrocarbon production in Russia are as follows:
- movement to the east, where there is almost no industrial and logistics infrastructure;
- movement to the north, where it is impossible to build the usual engineering and logistic structure, and climatic parameters are extreme in relation to all world analogues;
- increase in the gas content of hydrocarbon reserves.
Nowhere in the world is there a region with a simultaneous and such significant influence of the above trends on most of the industries associated with the production and circulation of hydrocarbons. Is Russia different from everyone else again? This is true, especially with regard to the technical aspects of industrial development in the Eastern Siberia and the Arctic. It’s not just climatic conditions. Logistic chains of raw materials and products are so unusual that the search for other routes that are not used in world practice seems inevitable.
Large technological projects in recent years, such as the Amur Gas Chemical Complex, ZapSibNeftekhim, Ust-Kutsk Polymer Plant, and logistics projects, such as Power of Siberia, the Sabetta port and a logistics complex in Yamal, are built in places where extreme placement parameters are nevertheless combined with several local advantages, which allowed to achieve economic feasibility due to the maximum enlargement of the processing and transportation values.
But the list
of such places with a combination of advantages has obviously dried up. Our
country, of course, is huge, but it is not endless either.
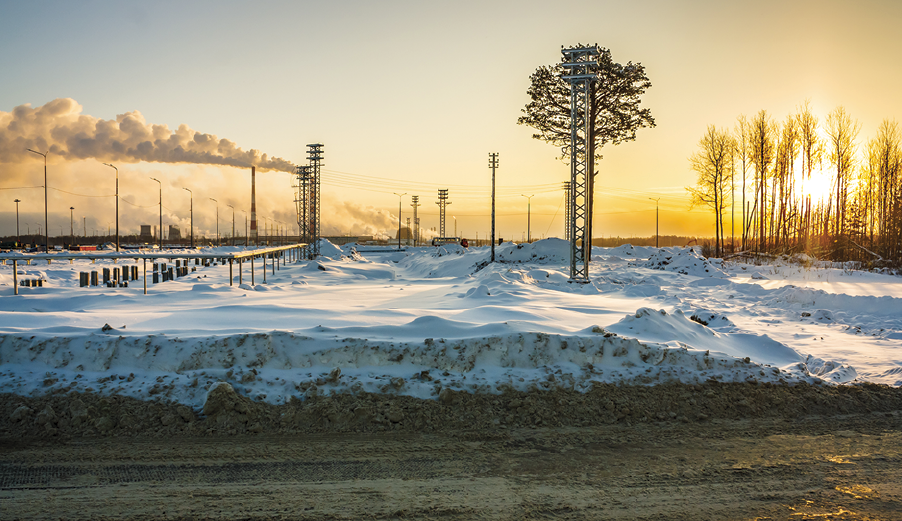
Source: andRU72 / Depositphotos.com
Gas chemistry: modern and timely
The global hydrocarbon community is, of course, restless in anticipation of the biggest changes in the last century. It’s no joke, mining giants are already seriously investing not only in the decarbonisation of hydrocarbon sources, but also in renewable energy. The world is clearly preparing to be different. Among the high decibels of information noise about the new image of a bright energy future, the voice of a completely new, but very unusual direction of development – gas chemistry – is more and more clearly traced.
The current interest in gas chemistry is due to several reasons:
- an increase in the gas factors of raw materials enhances the logic of shifting processing towards production facilities;
- the tendency of an increase in the cost of transporting gas products with a simultaneous technological reduction in the cost of deep processing;
- gas chemical processes provide an opportunity to reduce the “carbon footprint” of products.
Gas chemistry (although there are other interpretations) is usually understood as the processing of gaseous, under normal conditions, types of hydrocarbon raw materials into final production products. This area of competence in the division of labour in the oil business has always been upstream. But considering the above factors, it is gradually moving, and somewhere it is already located, in Downstream – the selection criteria are so different in the new realities of production. It became necessary to combine gas chemistry processes with the configuration of production facilities already in the early stages of development of serious projects.
Are there
alternatives to the development of gas chemical processes in the world and in
the Russian Federation? They certainly are in the world. There are many ways to
obtain products, and the most efficient one is found by assessing a huge number
of technological possibilities. But in Russia there is simply no comparable
alternative in very many cases, and cannot be. And that is why:
- very high content of the gas part in the balance of predicted raw materials;
- long distances between mining sites;
- a large number of relatively small single quantities of raw gas and illiquid fractions.
In combination with the general problem of logistics and all engineering parameters of remote accommodation facilities, there is an obvious need to organize at least some, but rather deep processing on site. The enlargement of the unit capacity, even with a significant increase in the depth of processing and, accordingly, the price of products, dictates the need for systems for collecting raw materials, which completely eats up all the advantages of this path.
The average distance between mining clusters in the Eastern Siberia today is about 300-400 km, in the Arctic zone and in Yamal – 1 50-300 km. Herewith, the average values of productivity on mining pads are usually not higher than comparable values in other regions at the beginning of their development, and sometimes significantly lower. The cost of laying 1 km of the onshore section of the pipeline is 2-4 times higher than the values for Western Siberia, and in the Arctic locations the multiplier can reach values of one to a dozen and a half. Therefore, even the construction of food routes will not ensure the efficiency of such facilities.
In terms of the product export and sale, even the construction of large port facilities – the way to save many facilities in almost all southern regions – does not in itself bode well for significant prospects. The very cost of such structures is very high. But the offshore logistics structure does not solve the problem of the illiquid part of gas raw materials. It turns out to be a rather unusual situation: the cost of an engineering solution to the issue of liquidity of the gas part is so much higher than its final price, which makes the oil part of the production incapable of pulling the project into the profitability zone. A paradox?
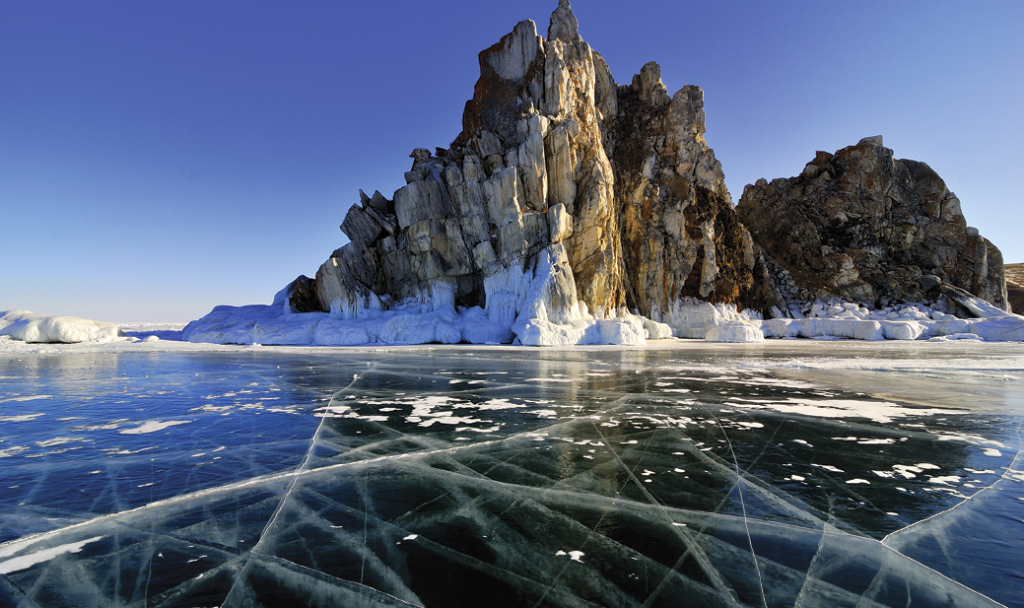
Source: shkonst / Depositphotos.com
At the top level, the solution looks pretty simple and consists of just a few things:
In terms of the product export and sale, even the construction of large port facilities – the way to save many facilities in almost all southern regions – does not in itself bode well for significant prospects. The very cost of such structures is very high. But the offshore logistics structure does not solve the problem of the illiquid part of gas raw materials. It turns out to be a rather unusual situation: the cost of an engineering solution to the issue of liquidity of the gas part is so much higher than its final price, which makes the oil part of the production incapable of pulling the project into the profitability zone. A paradox?
At the top level, the solution looks pretty simple and consists of just a few things:
- • it is necessary to increase the cost of products from gas raw materials by deepening processing;
- • you shall not increase the capacity, on the contrary, you shall look for processes in which it is possible to achieve adequate efficiency in relatively small technological volumes;
- • it is necessary to look for ways of mutual influence of factors, applied processes and logistic paths, including opportunities for decarbonization – only the presence of synergy of such factors will allow achieving reasonable economic values in such unusual conditions.
A new way of looking at things: which processes and products are required and which are not?
To demonstrate the possibilities of gas chemistry in the new realities of the circulation of hydrocarbon raw materials, a path of step-by-step progress from the upper-level postulates to the implementation of more specific assessments of the chains of redistribution is proposed.
Each substance or compound has an individual energy characteristic – the enthalpy of formation. Comparing the ΔHf values of potential raw materials and final products, one can see the inevitable costs of each of the redistributions.
While exploring possible ways of redistribution and chemical transformations, it is logical not to discount the possibility of producing hydrogen at the same time – one of the most important ways to decarbonize the final product, and hence its liquidity.
Of course, one should not forget about the carbon footprint of any output product. In this matter, very tough economic measures are expected in the very near future. This topic is discussed in detail in the article [1].
Here and below, of course, not all possible paths of chemical transformations and redistributions based on them are presented. The purpose of the article is only to demonstrate an approach to the selection and initial assessment of various options.
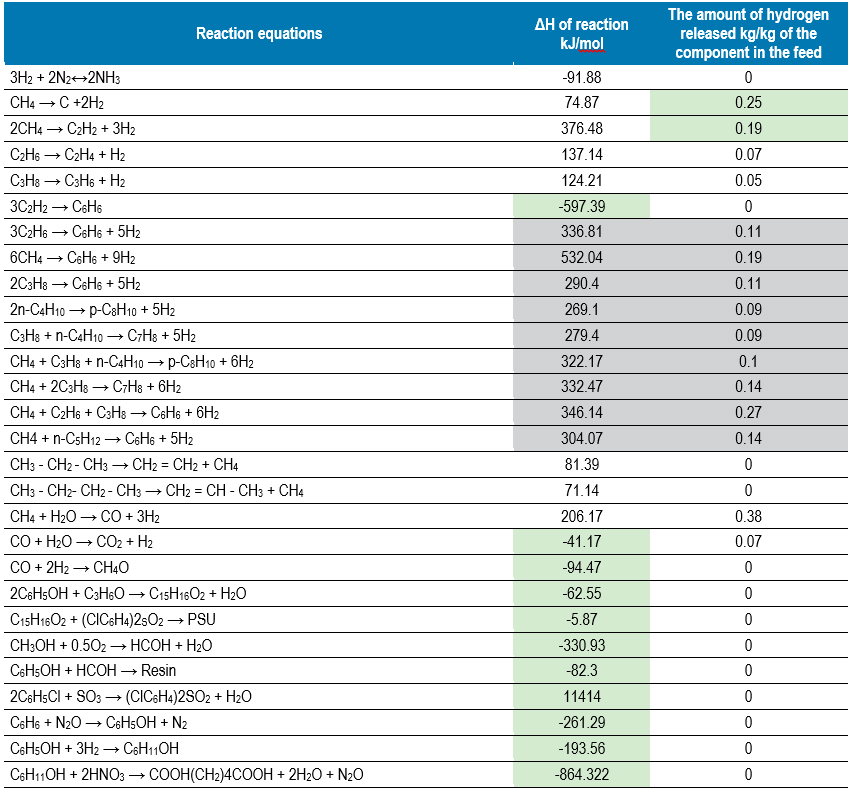
The data in Table 1 show that the most interesting from the point of view of the energy component are such processes as (their indicators are highlighted in green): the production of benzene, bisphenol-A, methanol, and from the point of view of obtaining hydrogen resources in the process, the pyrolysis of methane is certainly the leader.
Among the options and examples, we will not consider ammonia, which is an extremely interesting energy carrier and a possible source of a number of derivatives. But the amine path deserves a separate long article.
These energy carriers show more and more intensive in world practice, quite a lot has been written on this topic, but we are exploring simpler and more understandable chains to demonstrate the methodology and the very approach to working out specific options.
We shall also pay special attention to the reactions highlighted in grey. All of them require energy costs, but not too significant. Moreover, all these transformations serve as significant sources of hydrogen.
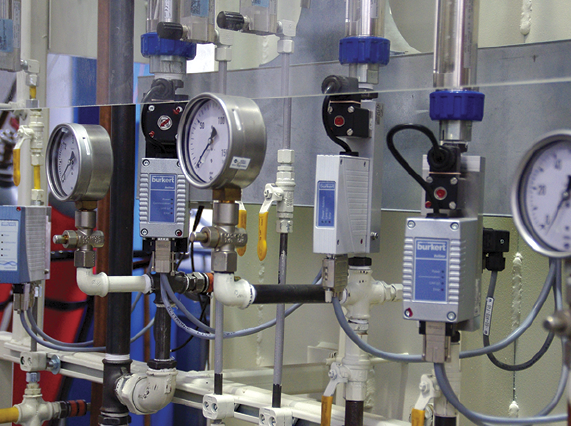
Source: dmaeuropa.com
This group of reactions of the processes of aromatisation of the components of associated petroleum gas with obtaining, as a rule, a mixture of OPF (benzene, toluene, xylene).
For further reasoning, for now, we will use the usual logic of project advancement. Table 2 and below shows a brief description of the processes for obtaining the selected ways of obtaining products.
Next, we present a brief description of some gas chemistry processes that are relevant to consideration under the conditions under consideration, with the characteristics most important for their selection in the local implementation option:
- APG in OPF (benzene, toluene, xylene) is a one-stage catalytic process for producing a mixture of aromatic hydrocarbons (benzene, toluene, xylenes, C9 fraction, C10 + fraction above, consisting mainly of naphthalene hydrocarbons) from light hydrocarbon feedstock, which is mainly C2 hydrocarbons -C5 with CH4 involved in the aromatisation process (up to 10%) [2].
Depending on the composition of the initial hydrocarbon gases and the mode of carrying out the catalytic process in relation to the needs of consumers, a concentrate of aromatic hydrocarbons with different content of components can be obtained. The process can be implemented at small-sized units (SSU) located directly in the areas of gas and oil production, at oil treatment plants (OTP), gas treatment plants (GTP), and complex gas treatment units (CGTU). The flexible technology of the process also allows to use it as part of petrochemical industries, for example, as part of LHG and NGL pyrolysis units to obtain additional amounts of aromatic hydrocarbons from the ethane-propane fraction formed in the Arkon process, which is an ideal pyrolysis feedstock for obtaining monomers.
The unit includes a reactor block, a block for separation and stabilisation of catalysis products, a membrane block for producing technical nitrogen for purging and regenerating a catalyst, and a unit for oxidative regeneration of a catalyst with a nitrogen-air mixture in a circulation loop. The reaction section includes two parallel lines (each of them has two reactors connected in series), one of which is in operation, one is being regenerated. - Ethane production. The schematic diagram of the installation can be described as follows. Raw materials mixed with steam (volumetric ratio “raw material – steam”, 7-9: 1) is heated in several parallel pyrolysis furnaces to 800-900 °C, where a strongly endothermic dehydrogenation reaction occurs at a pressure below atmospheric (0.01-0.02 MPa). After passing through the furnace, the reaction mixture is cooled in a quenching evaporator to 370-420 °C. The unit is used to generate steam, which transfers energy to the turbocharger. After undergoing preliminary compression, the reaction mixture is separated in one or more rectification columns to obtain an ethane-ethylene mixture and by-products.
- Dehydrogenation of propane to propylene. The Catofin technology is the conversion of propane to propylene by dehydrogenation in one stage in a group of horizontal adiabatic reactors operating in parallel on a fixed bed of Cr2O3/Y-Al2O3 catalyst.The reactors operate in the “reaction – regeneration” modes.The working cycle lasts about 20-30 minutes.The process takes place at 560-610 °C and 0.3-0.5 kPa.Propane conversion varies within 45-50%, the propylene selectivity varies within 82-87 %. The continuity of the process is ensured by the presence of at least three parallel reactors. Heat is supplied to the reaction zone with the feed, and the heat obtained by the catalyst at the stage of regeneration is also used, which is performed in several stages: blowing with superheated steam; burning of coke with a mixture of air and methane [4–5]. The duration of the dehydrogenation cycle is limited by the amount of heat accumulated by the catalyst, since the reaction is highly endothermic. With the availability of raw materials isobutane allows the production of isobutylene.
- Partial oxidation of methane. The process takes place at a temperature of 1500 °C. Raw materials and oxygen, having passed a separate preheating, are fed to the burner. Having passed the mixing zones, they are fed into the reaction zone, where they are ignited. The mixture formed at the outlet of the reaction zone is rapidly cooled (with water or oil). Water cooling is the simplest option, but less thermally efficient than oil cooling. Cooling with light hydrocarbons can serve as an alternative, which will lead to the formation of additional amounts of acetylene and ethylene in the temperature range of 1500–800 °С. This process is usually referred to as a two-stage process [6]. The product mixture consists of acetylene and products of partial combustion of raw materials. Light hydrocarbons from methane to naphtha can be used as raw materials.
- Phenol-formaldehyde resin production. In the traditional novolac process, molten phenol is loaded into a stirred reactor followed by an acid catalyst (sulphuric acid, sulphonic acid, oxalic acid). The formaldehyde solution is added at about 90 °C. The formaldehyde – phenol ratio is maintained at the level of 0.75–0.85:
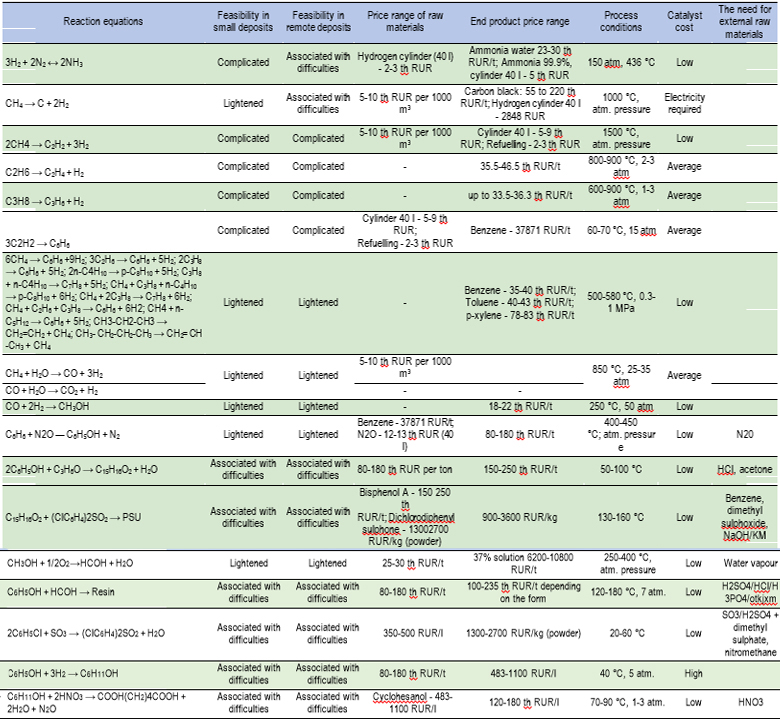
- The reaction proceeds with the release of heat, which is removed by means of water mixed with formaldehyde. This solution, when it enters the reactor, evaporates and, condensing in the refrigerator, is fed back to the reactor. Besides water, toluene or xylene can be used. The reaction is complete after 6-8 hours at 95 °C. Further, there is a vacuum cleaning from water, free phenol and other volatile substances at 140-160 °C. Oxalic acid does not require neutralisation, decomposing into CO, СО2 and water. Sulphuric and sulphonic acids require lime neutralisation [7].
Polysulphone production. The commercial synthesis of polysulphones is performed by nucleophilic substitution polycondensation, which involves the reaction of bisphenol A with 4,4-dichlorodiphenylfulfone in a bipolar aprotic solvent in the presence of an alkaline base. Such a solvent can be: 4methyl-2-pyrrolidinone, dimethylacetamide, sulpholane and dimethylsulphoxide. Following substances may be applied as an alkaline base: sodium and potassium hydroxides, potassium carbonate. Reacting in a mixture with an alkali, bisphenol forms a bisphenol salt, which in turn reacts with 4,4-dichlorodiphenylsulphone to form polysulphone (PSF/PSU). The typical temperature range for polysulphone polymerisation is 130–160 °C [8]. Ref Fig. 1.
Trimerization of acetylene. This is one way of producing benzene. The process takes place with a nickel catalyst in a temperature range of 65-75 °C at a pressure of 15 atm. In this case, the yield of benzene is 88%, and the yield of styrene, the by-product, is 12% [9, 10]. The process is not widely used in industrial production, since alternative technologies in conjunction with existing deep oil refining processes are more efficient.
Methane pyrolysis. The process can be performed in various technological conditions depending on the goals and required forms of carbon production. It can be performed in a conventional reactor for the pyrolysis process, as well as in several versions of plasma reactors. In general, the process is performed at temperatures ranging within 800–1200 °C at pressure of 0.5–10 bar.
The process makes it possible to obtain carbon nanotubes of various shapes and lengths, as well as other types of carbon materials. Despite the need to burn part of the fuel to generate electricity, plasma pyrolysis of methane can reduce СО2 emissions into the atmosphere by more than 2 times, compared with alternative methods of producing similar products [11].
The processes of pyrolysis of methane and APG have long been given considerable attention. However, in recent years, more and more end-use options have been found for the resulting carbon products. For example, there are already technologies for producing fibres from them. An interesting fact is that until recently, a significant amount of hydrogen formed in these processes was attributed to by-products.
About hydrogen – how can it be without it?
Increasing attention on the agenda of discussions, both at the interstate and intracorporate levels, is given to decarbonization issues and the development of innovative approaches to the production and use of hydrogen energy, as one of the most promising ways to reduce the carbon footprint, which has a high potential as an energy carrier.
International strategies are developing various financial levers and incentives to promote energy decarbonization. So, in 2018, there were about 50 measures supporting the energy use of hydrogen mainly in logistics, and by 2020 the focus has shifted to industry and energy. A number of countries have already organized partnerships for the development of hydrogen energy technologies, in particular, Australia jointly with Japan organized a pilot project to create a hydrogen supply chain, and cooperate with Korea in the field of export and import of hydrogen.
However, the technical capabilities of the current stage of development of hydrogen energy are associated with the low competitiveness of the proposed developments, high production costs, difficulties in storage and logistics of hydrogen to the consumer. The main demand will be for commercially cheap technologies that are simple enough to manufacture and implement.
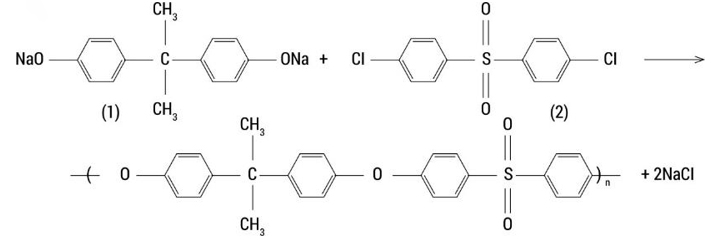
Currently, the most efficient way to produce hydrogen is either from natural gas or coal (grey hydrogen) using carbon capture and storage (CCS) technologies (blue hydrogen), or electrolysis using electricity with a low carbon footprint (“green” hydrogen).
The main advantage of hydrogen is clear: when it is burned, no СО2 is formed, however, the amount of NOx emissions exceeds similar emissions from burning natural gas. Also, hydrogen has a high potential for use as a means of energy storage, which is especially important for the growing share of RES.
According to experts, in the near future the need for hydrogen production will increase several times, and “green” energy not only will not be able to satisfy the need for such volumes, but remains quite costly. Thus, pursuant to IRENA estimates for 2019, the cost of 1 kg of hydrogen based on wind energy is on average about USD 4, solar – almost USD 7, from coal or gas it costs USD 1.5-2.5 (even considering CCS) and this gap will not disappear in the next 10-15 years.
In the current conditions of interstate support, the promotion of hydrogen technologies, especially the production of “grey” and “blue” hydrogen from fossil raw materials, becomes urgent. One of the most developed and cost-efficient methods for obtaining such a promising energy resource are gas-chemical methods for utilizing natural gas and APG, the advantage of which is not only a decrease in the share of flared valuable hydrocarbon resources, but also the production of highly liquid products that can be used directly in the field.
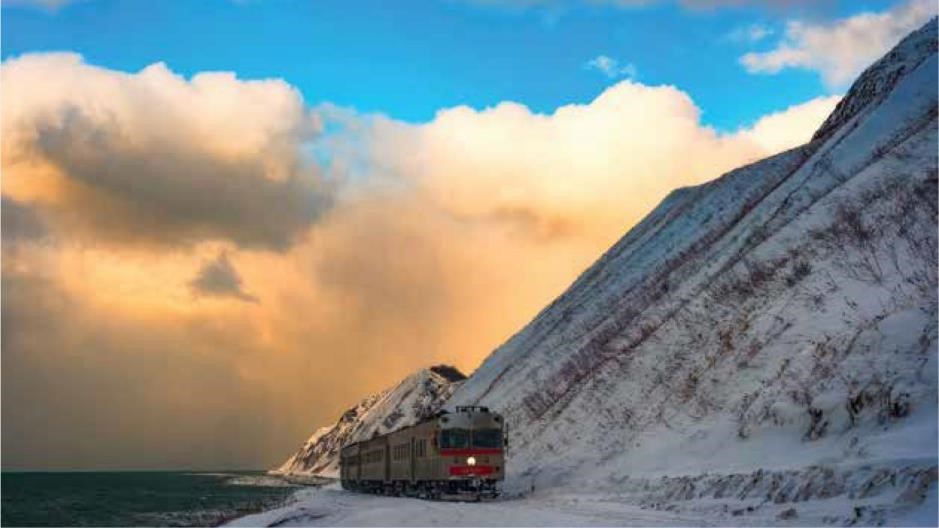
Source: VladimirE/depositphotos.com
According to preliminary estimates of the Rosatom State Corporation, the scheme of hydrogen production by the method of steam reforming of methane using high-potential heat of the promising HTGR-200 reactor plant allows to produce hydrogen with a weighted average cost estimated at the start of the project at a discount rate of 7%, in the range 1.85-2.35 USD/kg excluding its storage and delivery, depending on the price of consumed natural gas from 4260 RUR/th cub.m up to 9000 RUR/th cub.m.
What is the current status and prospects for the development of hydrogen energy in Russia? Isn’t it obvious that, considering the climatic and geographic specifics of our immense distances between production and infrastructure, multiplied by infrastructural features, hydrogen should be both extracted and directly used precisely closer to its original sources?
Several conclusions may be suggested:
- to reduce the carbon footprint of products, hydrogen energy should be used at production sites, especially where there are illiquid hydrocarbon resources;
- low-liquid hydrocarbon resources, mainly gas, and its share in the production balance is rapidly increasing – the main source for the hydrogen energy of the Russian Federation;
- most preferable is the use of gas chemical technologies, in which hydrogen is evolved as a by-product.
And there is no need to store energy by chemical methods with its inevitable losses during transformations. It is easy to use in the production of products on the spot. Which ones? Least energy consuming and most valuable. But, considering the remoteness, they are quite simple to implement.
Herewith, redistributions with initially high unit costs associated with relatively small volumes may turn out to be quite efficient due to the action of other factors mentioned above.
Selection criteria: is everything anew?
A significant variety of processes, the invariance of the choice of products and redistributions form a serious task of building an optimal production chain. Within the framework of the results presented in this article, when justifying the choice of the technological chain, the assessment method developed by the Scientific and Technical Centre Gazconsulting was applied.
The assessment establishes the need to ensure such an organisation of the technological process, which ensures the most efficient use of its elements (individual processes). The quantitative and qualitative assessment of such readiness is based on the developed mathematical model, which formally describes the main processes and functions of the sequence of technological processes and is based on the use of logical-probabilistic methods for the formalized representation of the state of the production chain by a Boolean function of the state and its individual elements at the considered moment in time.
The logic for evaluating processes and redistributions is built in the following sequence of actions:
- Formation of a set of factors that allow for a comparative assessment of the processes under consideration.
- Establishment of limiting values and assumptions in relation to particular cases of these factors.
- Directly evaluating values.
The development of such a model was due to the need to solve the problems of choosing the optimal sequence for performing technological processes, in which the entire chain remains ready to perform the given functional tasks. Herewith, it is dynamic in nature and has more general properties, providing optimisation tasks for assessing the functional readiness of both individual elements (processes) and the production chain as a whole.
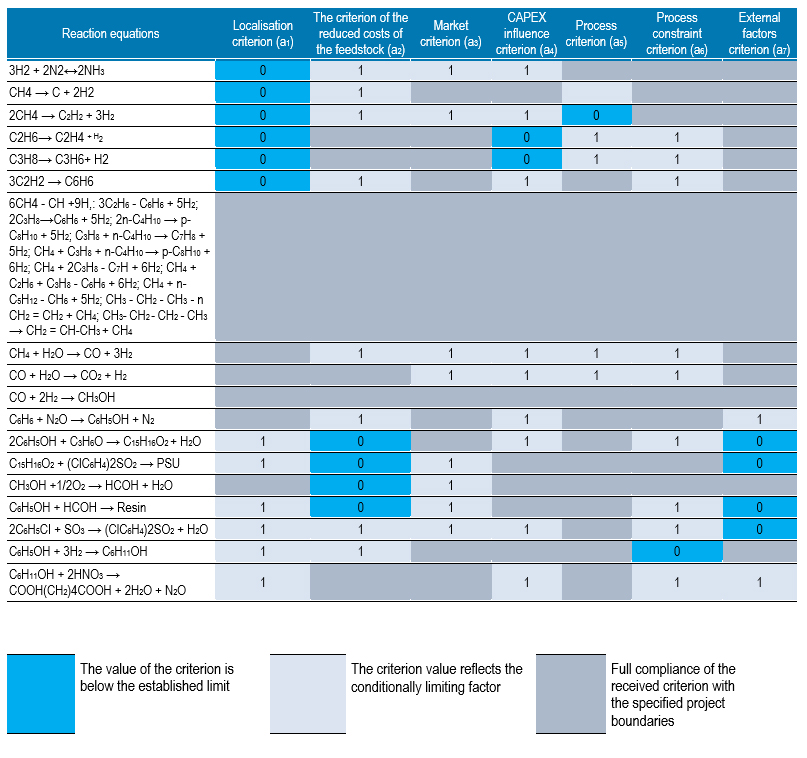
Source: the data in the table are generated automatically on the basis of an automated model for calculating the readiness of technological processes for implementation under specified conditions, developed by the company “STC” Gazconsulting”
The process of modelling the functional readiness of such a system Y (t) will depend on the value of the impact x1(t),…, xn(t) and modelling processes in blocks a1(t),…, aN(t) at the same moment (t), and also on their values at some previous moments, the number of which is assumed to be finite. The dependence of the output modelling process on influences and competitive processes in its blocks will be:
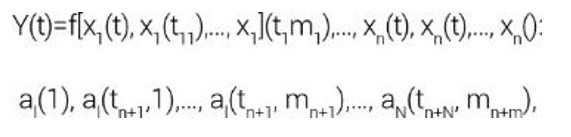
where f is a modelling operator of systems in the form of a Boolean function, t is the current moment in time, and tij(tij<t) are the previous moments in which the values of actions and states of blocks affect the functional state of the output of the entire production chain at the current moment “t”.
Let us present the obtained comparative assessment of the factors (table 3), which gives an idea of the reasonableness of the further use of a particular process in the design of the production chain, as well as the final comparative table of the obtained values of Y (t) in relation to the production chains being built (table 4).
The preliminary assessment allowed to exclude a number of technological processes from further analysis and dwell in their calculations only on those whose implementation is achieved considering the minimisation of risks and costs, and also allows keeping the project within the planned economic parameters or higher.
On the basis of an automated computational model, indicators of the functional readiness of such a production chain Y (t) were obtained, and priorities for conducting a pre-project assessment were determined (Table 4), among which there were chains with a value of more than 0.75.
A landscape of opportunities
Obviously, for serious assessments, much deeper studies and calculations are required. However, with such a significant number of options and sub-options, each of which can either “pull” the project into the payback zone, or, conversely, drown it, such calculations are hardly possible to carry out in compliance with the usual criteria of cost engineering and other applied practices.
Our small study is aimed at demonstrating a new approach and new technological opportunities that open up when using a methodology that considers not only the paths and product conversions that have been beaten in world practice, but also alternatives in the modern realities of the Russian mining industry:
- the influence of balance factors (the amount of the gas part in reserves and the specific component composition), location and logistics factors dictate the use of other dependencies to determine efficiency than the determination of unit costs in relation to product prices;
- the possibility of using products in the immediate vicinity of their origin, the magnitude of the formation of by-products, the complexity of implementation in specific conditions, other specific parameters of each technological path often have a greater impact on efficiency than the values of capital and operating costs;
- the possibility, magnitude and share of the use of hydrogen energy directly in the production of products under the new paradigm can play a decisive role in the issue of the expediency of a particular production.
The proposed options are calculated using the dataset at our disposal for one of the significant deposit development projects in the northern region of the Russian Federation. Analysis shows that the resulting product line – monomers, polymers, organic synthesis products – may well lead to the selection of processes that have not found wide application in world practice.
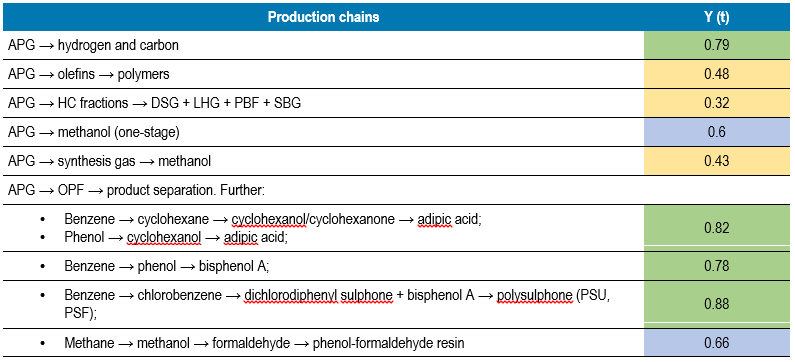
Moreover, it shall be borne in mind that the rapidly developing industry of using polymer and composite materials in all industries opens up individual opportunities for their efficient use directly in the region of origin, which certainly acts as an individual efficiency factor for each specific object. The use of modern methods of local production, such as 3D-printing, methods of extrusion and casting from various polymers, the use of hydrogen as an energy carrier to ensure production, undoubtedly include completely different prospects for the development of gas chemistry directly in the regions of production.
Due to the specific real conditions of modern hydrocarbon production in the Russian Federation, different approaches and tools are required for the technological design of facilities at the deposits. This is especially true for new significant hydrocarbon reserves located in the Eastern Siberia and the Arctic zone of Russia.