Irina IVANOVA
Professor, D.Sc. Sci., Chief Scientific employee, Moscow State Lomonosov University, Faculty of Chemistry
e-mail: iiivanova@phys.chem.msu.ru
Olga PONOMAREVA
Leading researcher, Ph.D. n., Moscow State University named after M.V. Lomonosov, chemical faculty
e-mail: oaponomareva@phys.chem.msu.ru
Egor ANDRIACO
Junior Researcher, Institute of Petrochemical Synthesis n.a. A. V. Topchiev RAS
e-mail: e.andriako@mail.ru
Nikolay NESTERENKO
R&D Program Manager for the conversion of natural gas in the company Total and Nanocleanenergy Laboratories at the National School of Engineering city of Cana (France), Ph.n.
e-mail: nikolai.nesterenko@total.com
Zeolite materials are critical in oil refining and petrochemical industry. Against the background of new environmental standards, the need to integrate the processes of oil refining and petrochemical industry, the growing role of the “closed cycle” economy and hydrogen energy, their contribution will only increase. Today these materials are of paramount importance for most key catalytic processes in petrochemicals. They are used in dehumidification, purification, СО2 absorption from combustion gases and allow reducing energy consumption for separation and purification and avoiding emissions into the atmosphere. The decarbonization of the industry, the need for recycling of waste and plastics, and the electrification of the industry will pose new challenges for the petrochemical industry, in which zeolites will be at the centre of attention.
The development of catalysts and the production of zeolite-based adsorbents will be a priority for the industry’s viability over the next 30 years and will play a key role in achieving zero emissions by 2050.
Refining and petrochemical technologies based on zeolite catalysts
The revolutionary breakthrough in petrochemical industry and oil refining, which occurred in the middle of the 20th century and led to a significant increase in efficiency, was associated with the implementation of zeolite catalysts and the creation of modern innovative technologies based on them. Currently, zeolites as catalyst components are used in more than half of modern petrochemical processes.
Zeolites are microporous crystalline aluminosilicates with a variable composition and pore size comparable to the size of petrochemical products (0.3-1.2 nm). The world production of synthetic zeolites in 2020 amounted to 2,200 th t, of which 18% are used as catalyst components [1]. The main advantages of zeolite-containing catalysts are environmental friendliness, chemical inertness, high chemical and thermal stability, wide variability of structures, form-selectivity, the possibility of changing properties by modification, duration of operation, manufacturability of use, as well as regenerability, i.e. restoration of activity by annealing coke.
In the oil refining industry, zeolites are used in catalytic cracking (FCC process, FAU and MFI zeolites) and hydrocracking (FAU zeolites), hydroisomerisation of С5-С6 paraffins (MOR), hydrodearomatisation (FAU, MFI), dewaxing and isodewaxing (MFI TON, AEL) (fig. 1). Technologies for olefin isomerisation (FER) and their oligomerisation (MFI, MTT) have been developed on the basis of zeolite-containing catalysts. In recent years, three technologies for solid-phase alkylation on zeolites have been developed and implemented: Alkyclean® (ABB Lummus-Albemarle), Eurofuel® (Lurgi-Sud Chemie), ExSact ® (Excelus).
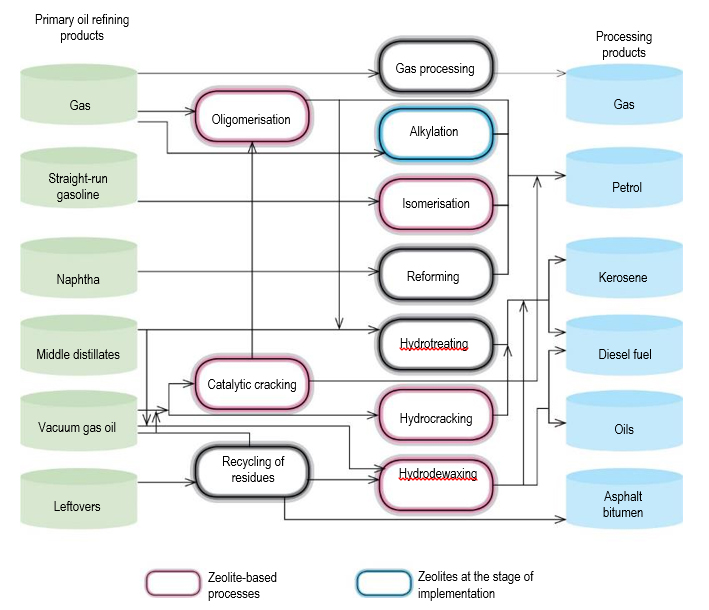
In petrochemistry and organic synthesis, zeolite catalysts are used in the alkylation of benzene with olefins leading to the production of cumene and ethylbenzene,
important precursors for the polymer industry, disproportionation of toluene (MWW, MOR, MFI) and isomerisation of the С8 fraction of alkylaromatic hydrocarbons (EUO, MOR, MFI) leading to the production of xylenes during the oxidation of propylene to propylene oxide (Ti-MFI), as well as in a number of others (Fig. 2). Replacement of liquid Friedel-Crafts acids or phosphoric acid on kieselguhr with zeolite-containing catalysts, on which alkylation was performed, and in most countries, including Russia, still carry out alkylation, allowed to solve a number of environmental, economic and technological problems associated with low selectivity, equipment corrosion, environmental pollution, large volume of waste water.
In the field of gas chemistry, an urgent task today is the development of zeolite-containing catalysts for the targeted processing of alkanes, which will allow replacing the pyrolytic processes of gas processing with catalytic ones, as well as the creation of new technologies for monetizing gas raw materials and obtaining valuable products for industry on its basis.
Currently, gas chemistry based on MFI and SAPO-34 zeolites has introduced processes for obtaining high-octane gasoline (Mobil), ethylene and propylene (UOP, Lurgi, DCIP, Sinopec, JGC, ExxonMobil) from natural gas through methanol/dimethyl ether, isomerisation of butene into isobutylene using FER, etc. [2]
State of affairs in Russia
In the Russian Federation, unlike other countries with a high level of oil and gas production, the share of the main secondary oil refining processes in the primary refining capacity is on average about 50%. Herewith, the total volume of secondary oil refining processes in Russia is several times lesser than in the leading countries of the world [3]. The solution to the problems of the development of the Russian petrochemical industry is laid down in the Plan for the Development of Gas and Petrochemistry for the Period up to 2030, approved by the order of the RF Ministry of Energy on 01.03.2012.
The key approach for fulfilling the tasks set for the industry is the implementation of new and enhancement of existing technologies, primarily based on the use of environmentally friendly solid zeolite-containing catalysts.
Until recently, the innovative development of the domestic petrochemical industry was based on the acquisition of ready-made technologies abroad based on imported catalysts. In recent years, the situation has changed somewhat.
In the field of oil refining, domestic cracking catalysts based on FAU and MFI zeolites and hydrocracking (FAU), leading to the production of gasoline and diesel fuel, have been developed, introduced or are at the stage of implementation. The main manufacturers of these catalysts in Russia are the Ishimbay Specialized Chemical Catalyst Plant (10 thousand tons per year with a capacity of 20 thousand tons per year) and Gazpromneft – Catalytic Systems (design production capacity of 15 thousand tons per year) [4].
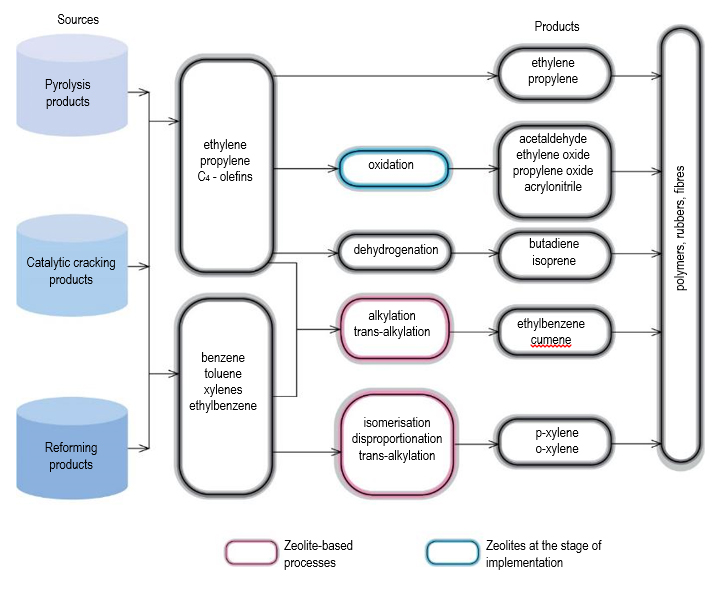
In 2017, a catalyst for the oligomerisation of butane-butylene fraction was introduced at the Gazprom Neft Moscow Refinery, which was developed jointly with specialists from UNISIT, created on the basis of the Kinetics and Catalysis Laboratory of the Chemistry Faculty of Moscow State University. The transition to a new catalyst allowed to increase the mileage and yield of the target product, and to reduce the number of regenerations. According to the estimates of the Moscow Refinery specialists, the annual effect from the use of the new oligomerisation catalyst will exceed 200 mln RUR.
A new hydrodewaxing catalyst (Gazprom Neft, All-Russian Research Institute for Oil Refining) based on MFI zeolite modified with a hydrogenating component has been developed and is being prepared for implementation. Work is underway to create a new technology for solid acid alkylation of the butane‑butylene fraction based on a zeolite-containing catalyst (TIPS RAS, Gazpromneft).
In the field of petrochemistry, work is underway to introduce technologies for the alkylation and isomerisation of aromatic hydrocarbons based on zeolite catalysts. In 2003, JSC Salavatnefteorgsintez introduced a domestic process for liquid-phase alkylation of benzene with ethylene, developed by the Institute of Petroleum Engineering of the RAS, Groz-NII and Salavatnefteorgsintez (the capacity in terms of ethylbenzene is 230 th t/year). The process is currently running on imported EBEMAX-1 catalyst based on MWW zeolite (Sud Chemie). Since 2010, SIBUR-Khimprom has been operating a unit for the alkylation of benzene with ethylene using the liquid-phase EBMax technology using MWW zeolite as a catalyst (the capacity for ethylbenzene is 220 th t/year). In 2018, Ufaorgsintez (Rosneft) completed the modernisation of the cumene production unit using ExxonMobil technology (170 th t/year). Work is underway to modernize cumene production at Omsk Rubber at Titan Group using ExxonMobil technology (165 th t/year), and it is also planned to modernize cumene production at Kazanorgsintez at Bisphenol A plant using MobilBadger technology utilising a zeolite catalyst MWW.
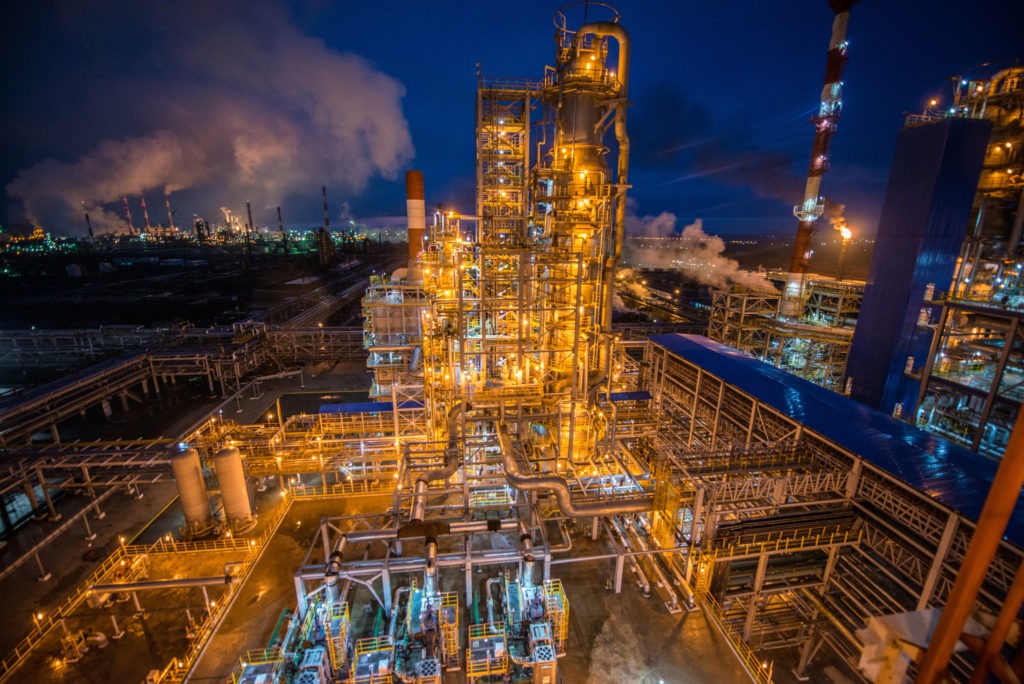
Source: vbashkortostane.gazprom.ru
The level of development of the gas chemical industry in the Russian Federation lags behind the advanced countries, only 5% of the produced gas is used as a raw material for secondary processing [5]. Processes based on zeolite-containing catalysts have not yet been implemented in Russia.
The quality of FAU zeolite produced in Russia meets world standards, but MFI zeolite’s properties are significantly inferior if compared with its imported counterparts. The MFI zeolites in the Russian Federation are mainly produced under the trademarks ZVK (ЦВК), ZVM (ЦВМ) and ZVN (ЦВМ) pursuant to domestic technology developed at VNIINP back in 1970-1980. While the world’s major manufacturers produce zeolites with a crystal size of 200-400 nm, the domestic enterprises supply the market with MFI zeolites with a crystal size of 2-5 µm. As a consequence, catalysts based on such zeolites are characterized by low efficiency, increased coke formation, as well as a high deactivation rate. The above factors significantly reduce the efficiency of domestic MFI zeolites as components of a cracking catalyst and preclude their use in oligomerisation and dewaxing processes. Currently, the annual demand of the Russian market for high-quality MFI high-silica zeolites to be used for cracking, oligomerisation, dewaxing, aromatisation, etc. is more than 500 t. As for the zeolite catalysts for petrochemical processes and organic synthesis processes based on high-silica medium-pore zeolites BEA, MWW, MOR, leading to the production of important monomers for the polymer industry – cumene, ethylbenzene, xylenes, they are not produced in Russia.
The need for a transition to new environmentally friendly technologies to ensure the sustainable development and progress of the oil refining, petrochemical and gas chemical industries requires the development of domestic technologies for the production of zeolites. Given the imposition of sanctions against Russia, this issue is becoming extremely urgent.
In 2019, within the framework of the program of the Foundation for Assistance to the Development of Small Forms of Enterprises in the Scientific and Technical Sphere, on the basis of the laboratory of kinetics and catalysis of Moscow State University, the company Zeolitika LLC was created, the purpose of which is to develop new modern technologies for the synthesis of domestic nanosized zeolites of various structural types BEA, MEL, MWW, etc.) and their production on an industrial scale to replace imported catalysts with domestic ones.
The research team proposed a new technology of vapour phase crystallisation in the absence of free water, the competitive advantages of which are the high quality of the obtained nano-sized zeolites, as well as the absence of liquid crystallisation waste, efficient use of the starting reagents and template, reduced crystallisation time, and reduced energy consumption [6].
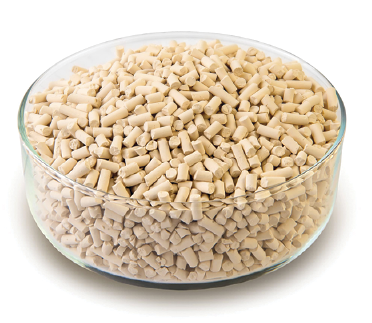
Source: himiya-ufa.ru
Transition to a new energy policy: innovations in the field of zeolite catalysis
Currently, humanity is on the verge of another revolution in the field of oil refining and petrochemical industry. The issues of rational use of natural resources, as well as the ever-increasing harm of anthropogenic impact on the world around us, are forcing humanity to a global revision of the approach to its activities. In the coming decades, a radical revision of the processes of petrochemical industry and oil refining will be performed with the increasing role of zeolite materials. Five main priority areas can be identified:
- Integration of oil refining and petrochemical industry.
- Operational efficiency and digital transformation (Industry 4.0).
- Decarbonization of petrochemical complexes and the “closed cycle” economy.
- Transition to new sources of raw materials, biomass conversion.
- Hydrogen energy and the renaissance of gas chemistry.
- It is assumed that zeolite catalysts will play a primary role in this transition.
Integration of petrochemical industry and oil refining
The growth in demand for basic petrochemical products is outstripping the growth in demand for fuel, so many enterprises, in order to maintain profitability, seek to create large petrochemical complexes that combine refineries and petrochemical complexes. According to Hydrocarbon Processing’s Construction Boxscore Database, there are currently about 470 major projects in the world to expand the capacity of petrochemical complexes worth USD 10 bln. The share of Russia and neighbouring countries accounts for about 55 projects (12%). Megaprojects for deep integration of refineries and petrochemical companies are gaining more and more popularity. These projects are aimed at increasing the yield of chemicals at refineries from traditional 10-15% to 45-53 % if taken in terms of weight. [7]. The implementation of such projects largely depends on the availability and readiness of new catalytic technologies. Most of these technologies are based on innovations in the field of zeolite catalysis in cracking processes (FCC, hydrocracking), in target petrochemicals (selective cracking of olefins, catalytic cracking of naphtha, dehydrocracking of naphtha, separation of linear and branched hydrocarbons, reverse isomerisation) and in the aromatic complex (new technologies for the production of xylenes).
There are five main integration strategies with the aim of increasing the yield of petroleum products at refineries by introducing “targeted petrochemical” technologies.
The first scheme includes the modernisation of the FCC complex by integrating it with the selective cracking of heavy olefins from the gasoline fraction to propylene. This scheme assumes optimisation of the zeolite catalyst for the FCC unit and results in much higher ethylene and propylene yields. The second strategy involves the implementation of a distillate hydrocracking process into light alkanes and naphtha, followed by the pyrolysis of alkanes to olefins and the conversion of naphtha to aromatic hydrocarbons. The next strategy is based on “molecular refining” on zeolites, including the separation of LHG into propane and butane, followed by their conversion to propylene and butenes, as well as the separation of linear and branched paraffins in naphtha, followed by isomerisation of branched hydrocarbons into linear ones and their pyrolysis into ethylene and propylene. As a result of this operation, only normal paraffins are converted in the pyrolysis unit, which increases the yield of light olefins by 10-15%.
The fourth strategy is associated with the implementation of the olefin metathesis process, which opens up wide opportunities for increasing the yield of ethylene and propylene. Finally, the fifth strategy is based on the catalytic (dehydro-) cracking of naphtha, which significantly increases the yield of propylene and ethylene compared to the pyrolysis process. The implementation of these strategies will increase the yield of oil products from 10-15% to 30-50%, which corresponds to a fully integrated complex.
The next stage of evolution will be the direct conversion of oil into petrochemical products by cracking. This option leads to lower production costs and СО2 emissions per ton of product. Currently, there are at least three strategies for implementing this stage. They are based on FCC, hydrocracking and pyrolysis processes. The selection of the scheme depends on the type of raw materials and the type of petroleum products that the plant is to produce. In all three cases, innovation in zeolite catalysis will play a fundamental role.
Operational efficiency and digital transformation (Industry 4.0)
Operational efficiency of production is based on reliability and detailed knowledge of the process and catalyst. Zeolite catalysts have been used in industry for over 60 years and have proven to be reliable, safe and efficient. However, the development of new zeolite-based technologies takes a long time, on average from 10 to 15 years, which is incompatible with the growing demand for these technologies. An increase in the speed of implementation of new developments can be achieved through the use of modelling, materials informatics and artificial intelligence. A prerequisite for the implementation of digital transformation technologies in this area is the creation of libraries of zeolite materials and catalysts, the training of specialists and the support of scientific schools in the field of zeolite catalysis.
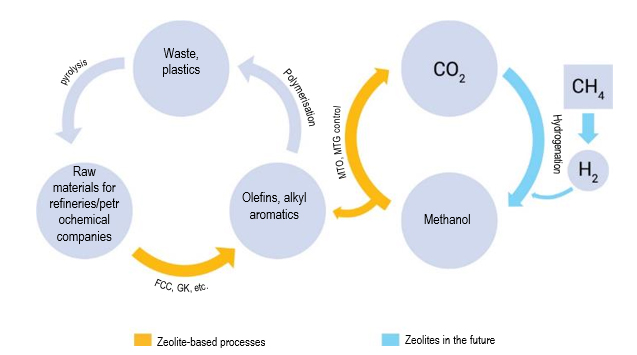
Decarbonization of petrochemical complexes and the “closed cycle” economy
In accordance with the 2015 Paris Climate Agreement, greenhouses gases, mainly carbon dioxide, and therefore, indirectly, the sources of its formation – oil, gas, and coal – are declared the main enemies of the climate. In world practice, at the initiative of the EU, a reporting system for the so-called “carbon footprint” is being implemented, in other words, in the production of any type of goods and services, greenhouse gas emissions will be assessed. The governments of almost every country in the world impose a carbon tax – a payment for the emissions of the equivalent of carbon dioxide into the atmosphere. According to the Russian Academy of Sciences, the financial losses of domestic exporters can reach 3-4 bln EUR per year.
Thus, for the Russian petrochemical industry it is necessary to reconsider the existing realities of export and raw material development. The development shall be based on the production of high-tech, high-quality products of higher value added on the basis of resource- and labour-saving environmentally friendly technologies.
First of all, it will be necessary to implement technologies for the carbon dioxide capturing, storage and processing.
Zeolite technologies will play a primary role in this regard [8]. First of all, zeolite materials can be used to capture СО2 from combustion gases at a low partial pressure of the components and purify it for subsequent transportation. The use of zeolites in separation processes will significantly reduce energy consumption and, accordingly, emissions of anthropogenic gases.
In addition, an important task will be to utilize СО2 by converting it into useful products. In this respect, “closed cycle” processes are promising. Currently, 2 such cycles are being considered, which are interconnected (Fig. 3). The most acceptable solution for the utilisation of СО2 would be its conversion to methanol. Methanol can find a large number of applications in the oil refining complex, but one of the most promising solutions will be its conversion to olefins, aromatic hydrocarbons and fuels (MTO, MTG processes).
The methanol production process will require the use of large amounts of hydrogen, which can also be obtained on the basis of zeolite technologies (paragraph 3.5).
Processes for the conversion of methanol to olefins and aromatic hydrocarbons are very promising due to a significant increase in demand for plastics obtained from these monomers. The production of plastics from methanol will solve the problem of the “closed cycle economy”, which is one of the most important challenges for the petrochemical industry today.
Waste from the use of plastics is increasingly seen as one of the main sources of pollution and ensuring its efficient recycling is essential for the industry to survive. The most optimum direction of such processing will be thermal pyrolysis, the products of which will be processed at integrated petrochemical complexes, at FCC and hydrocracking units on zeolite catalysts, resulting in olefins and aromatic hydrocarbons required for the synthesis of plastics. Zeolites will thus continue to play a primary role in closed cycle processes.
Another aspect of the closed cycle economy is the electrification of hydrocarbon conversion. Currently, most of the furnaces, compressors and steam generators in refineries use hydrocarbons as fuel. The combustion of these products produces СО2-containing gases. Amine absorption is not efficient for these types of streams and the capture of carbon dioxide from them is very expensive. Therefore, one of the current trends is the replacement of fuel heating elements with electric ones, in which energy will be supplied to the reactor volume.
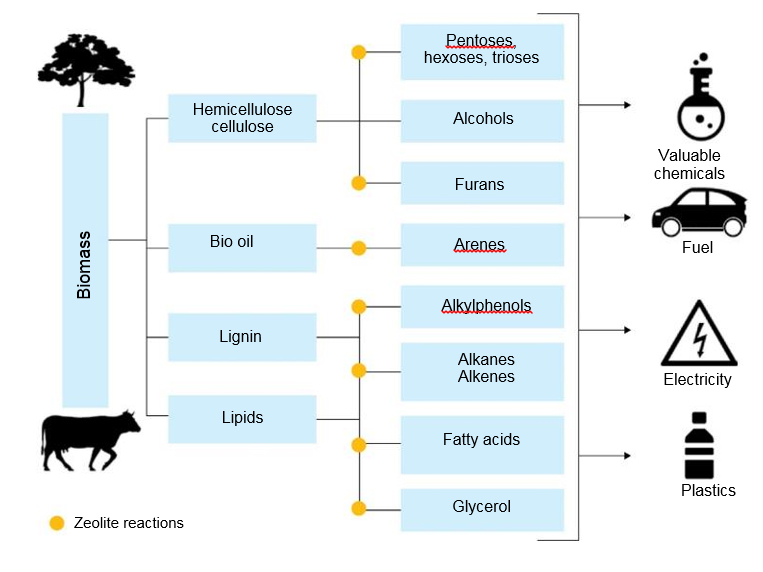
In other words, it is not the walls of the reactor that will be heated, but the catalyst. It will also greatly simplify regeneration and reduce system inertia. A new generation of zeolite-based catalysts must be developed for these types of installations.
Transition to new sources of raw materials, biomass conversion
The growing demand for biofuels is driven by several key reasons, the first of which is that bioresources are renewable and CO2 neutral, unlike fossil fuels. The use of biomass for the production of fuels and chemicals can lead to partial replacement of fossil resources with renewable sources. In the last decade, many states have allocated large resources to create technologies for the processing of biomass [9].
Like oil, the biomass consists of high molecular weight components. The main sources of biomass are lignocellulose and lipids, which contain triglycerides from vegetable animal fats and microalgae. Of these, the most common is lignocellulosic biomass, consisting of cellulose, hemicellulose and lignin. In addition, there is a smaller group of animal or vegetable protein fractions. The biomass processing scheme is shown in Fig. 4.
The main purpose of biomass valorization is to reduce molecular weight.
By analogy with oil conversion processes, catalytic cracking processes on zeolite catalysts can be used here. Fats and oils with long linear hydrocarbon chains are structurally the closest to petrochemical hydrocarbons; therefore, zeolites are used in these processes with great success. However, it should be expected that the mechanisms of transformation of bulky biomass substrates containing a large amount of oxygen are more complex and require the creation of new catalytic systems [10]. A number of companies have developed direct cracking processes in dry biomass FCC units. Co-processing in FCC or hydrocracking units of petroleum feedstocks with bio-feeds that have passed the stages of partial hydrogenation or thermal pyrolysis is the optimal solution in many cases. It also avoids additional investment and significant changes in operating arrangements.
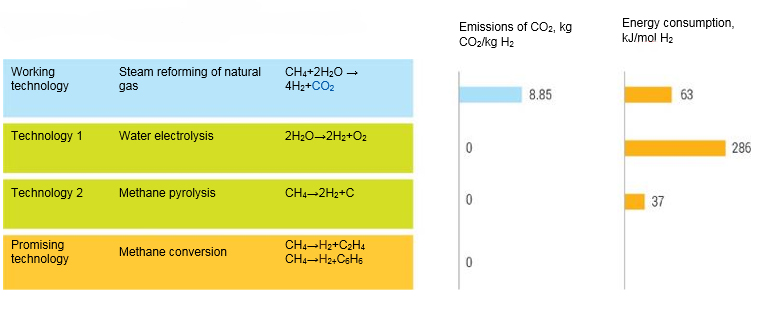
Another interesting option is the conversion of alcohols. Ethanol and butanol are now produced in large quantities from renewable sources. Besides their use as biofuels, the conversion of bioethanol and biobutanol into valuable chemicals is becoming increasingly attractive. Promising technologies include the conversion of ethanol to ethylene, propylene and butadiene, and the conversion of butanol to butenes, light olefins, and aromatic hydrocarbons. Effective zeolite catalysts have been developed for these processes.
Hydrogen energy and the renaissance of gas chemistry
Hydrogen is a high-energy product and can be used both for the internal needs of petrochemical complexes and for the conversion of CO2. Today the main method of hydrogen production is steam reforming. However, this method results in the release of 9.3 tons of СО2 per ton of hydrogen, which requires capture and the appropriate infrastructure for this (Fig. 5). An alternative technology based on electrolysis of water absorbs 5 times more energy per ton of hydrogen. In this regard, direct decarbonization of natural gas into carbon, olefins or aromatic hydrocarbons is becoming increasingly important for hydrogen power engineering. The first process has a serious drawback, as it leads to the formation of a large amount of coke, which has no market for sale.
Therefore, the processes of converting methane to hydrogen and olefins or aromatics are much more promising. These processes can be efficiently run using the zeolites. Many of these technologies are under development and will play a significant role in the petrochemical industry.
Moreover, the processes of hydrogen production by aromatisation of light alkanes, the proportion of which will increase due to the integration of petrochemical complexes, will be of increasing importance in the future. These processes are also based on zeolite catalysts (CICLAR (UOP), ALPHA (ASAHI), AROMAX (CHEVRON) processes).
Conclusion
An analysis of the prospects for the development of the petrochemical industry in the field of zeolite catalysis shows that the primary task here is the development and implementation of the domestic technology for the synthesis of nano-sized high-silica zeolites of the MFI, BEA, MWW and MOR structural types, which are necessary to support existing petrochemical plants.
Moreover, an urgent task is to create new zeolite catalysts and technologies to ensure the integration of refineries and petrochemical plants; creation of direct processes for the conversion of oil into valuable petrochemical products; implementation of closed cycle processes – conversion of CO2, waste and plastics into monomers and fuels; conversion of biomass into fuels and valuable chemical products, as well as conversion of methane into hydrogen and olefins or aromatic hydrocarbons. The implementation of these tasks will allow for the transition to a new energy policy.