Vladimir ARUTYUNOV
Member of NAS of Republic Armenia,
professor, Dr. Sci. in Chemistry, chief researcher,
N.N. Semenov Federal Research Center
for Chemical Physics, RAS, Institute
of Problems of Chemical Physics, RAS
e-mail: v_arutyunov@mail.ru
Introduction
The abundant resources of natural gas, including its unconventional varieties such as shale gas and gas hydrates, make them a long-term base for the global energy sector. Associated petroleum gas (APG) remains a significant raw material resource for the energy sector, the world volume of flaring of which, despite all efforts and legislative measures, has not decreased for many years, remaining at the level of 140 billion cubic meters. Biogas produced during the processing of various agricultural and household waste can also play a certain role in the local energy sector.
But combustible gases are not always a convenient energy source, especially for transport and remote consumers. Despite the constant growth in the consumption of compressed natural gas (CNG) in the transport sector and the expansion of small-scale production and distributed consumption of liquefied natural gas (LNG), they cannot fully assume the role of a universal energy carrier, which is currently played by oil and its liquid products. processing. Therefore, the problem of conversion of hydrocarbon gases of various composition and origin into a more convenient liquid fuel, as well as more environmentally attractive gaseous energy carriers, primarily hydrogen, is becoming more and more relevant.
Methods for converting natural gas into liquid hydrocarbons and more attractive types of gas engine fuels are well known, but the existing technologies are still unattractive for practical use, especially in domestic conditions and for small-scale enterprises [1, 2]. The reason is that the methane conversion, the main component of natural and associated gases, into other chemical products is an extremely complex and energy-consuming process.
Under normal conditions, methane is the most stable hydrocarbon with very strong chemical bonds, the rupture of which requires a lot of energy. This is the main reason for the serious difference between traditional petrochemical processes, in which rupture and isomerization of relatively weak C – C and C – H bonds in liquid hydrocarbons prevail, and gas chemistry, in which the initial process is the rupture of a very strong C – H bond in a methane molecule. Chemical processing of all other hydrocarbons, starting from ethane, requires much less effort, and can be attributed to well-developed traditional petrochemical processes.
The complexity of the implementation of the first stage of methane activation forces us to resort to bypass ways of its conversion, the most effective of which turned out to be its preliminary conversion into synthesis gas – a mixture of Н2 and СО molecules, for which effective catalytic processes of conversion into methanol, synthesis liquid hydrocarbons (SLHC, synthesis oil) and other products. The main advantage of this route is that, under certain conditions, methane can be almost completely converted into synthesis gas, but this requires high temperatures (~ 900 °C) and, consequently, significant energy consumption.
Traditional processes based on synthesis gas
Almost all modern industrial technologies for converting natural gas into chemical products, with the exception of halogenation and sulfidation processes, are based on its preliminary conversion into synthesis gas. Then, from synthesis gas, such large-scale chemical products as ammonia, hydrogen, methanol and synthesis liquid hydrocarbons are obtained, which are now considered as potential alternative energy carriers. Conversion of natural gas into synthesis gas is the most difficult and costly stage of modern gas chemical processes, which accounts for up to 60–70% of all costs for obtaining target products. High costs for this stage are the main factor restraining the development of modern gas chemistry.
The most common industrial process, on the basis of which more than 80% of synthesis gas is now produced, is the steam methane conversion.
СН4 + Н2О <-> СО + 3Н2
ΔН = +226 kJ/mol
This highly endothermic process, which produces hydrogen-rich synthesis gas with an Н2/ СО = 3 ratio, began to be widely implemented on an industrial scale since the 1960s, when natural gas was used as a feedstock instead of coal. Steam reforming is usually performed using relatively inexpensive nickel catalysts at temperatures of 800-1000 °C, pressures above 2 MPa, and a high Н2О/ СН4 ratio of 2.5-3.0 or more to reduce the catalyst carbonation. The process is performed in tube furnaces with external heating of reaction tubes filled with a deposited metal catalyst (Fig. 1).
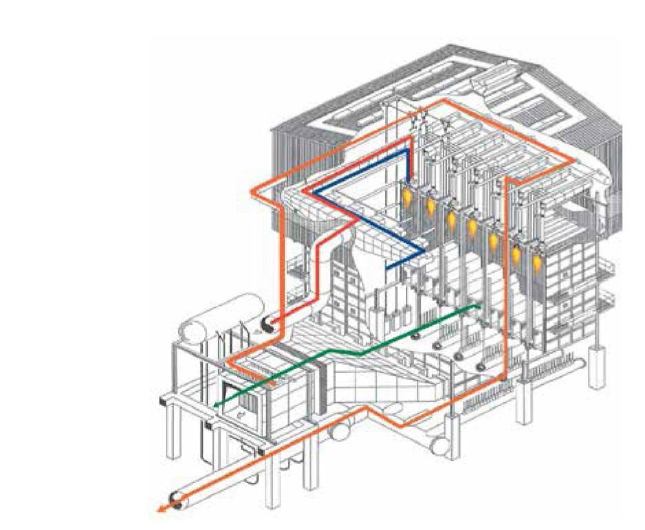
The leading companies developing the steam reforming process are Howe-Baker (USA), Haldor Topsoe (Denmark), Foster Wheeler Corp. (USA), Technip (France), Lurgi (Germany) and a number of others, the designs of reactor furnaces (reformers) of which differ mainly in the heating schemes of reactor tubes with a catalyst. The heat from the flue gas is used for the production of steam and for the preheating of the raw materials and the air supplied to the burners. If there are many heavy methane homologues in the feedstock, leading to accelerated carbonization of the catalyst, then a preliminary reforming reactor is included in the process scheme, in which steam conversion of heavy methane homologues into methane and partly into synthesis gas is performed at temperatures up to 600 °C.
A promising direction in the technology of steam reforming of natural gas, especially from the point of view of reducing emissions of the main greenhouse gas CO2, is the use of high-temperature helium nuclear reactors (HTGR) as a heat source – a new type of universal nuclear energy sources capable of generating heat with temperatures up to 1000 °C. The Rosenergoatom Concern participated in the development of a project providing the deployment of the plant with a HTGR series MGR-T modular reactor for the production of hydrogen and electricity (the unit thermal power is 600 MW). The reactor was tested in the technology of combined generation of high-grade heat with a coolant temperature at the outlet of the reactor 950–1000 оС and electricity with a gas turbine energy conversion cycle efficiency of 48%. The high-potential heat obtained in the reactor is removed by the primary coolant (helium), which has a temperature of 950оС at the outlet of the reactor.
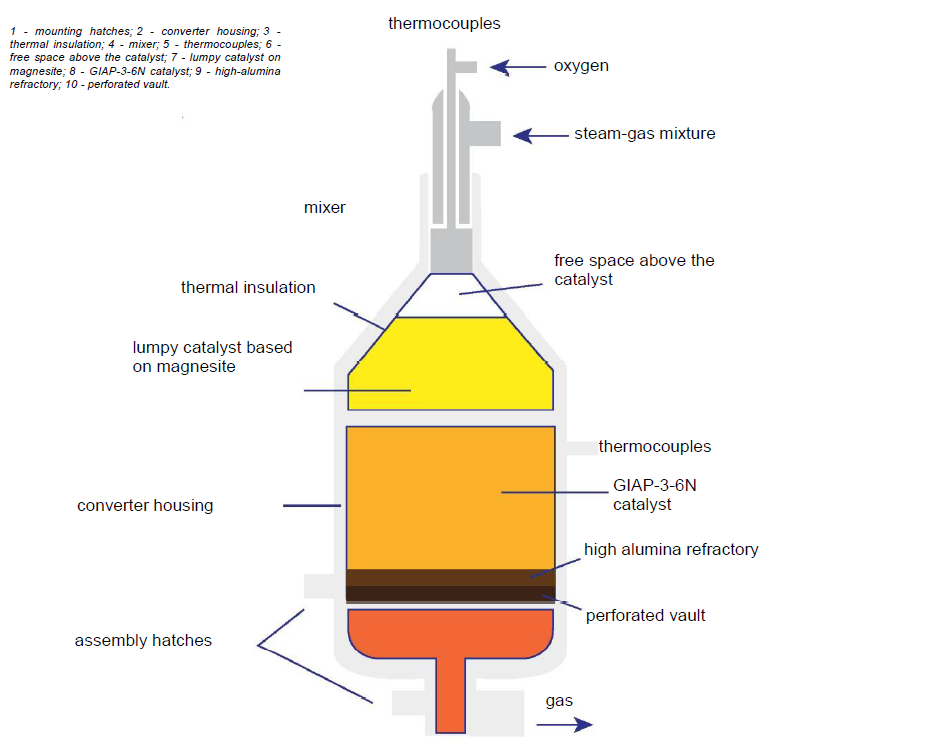
This heat is transferred to the converted steam-gas mixture in the chemical-technological part of the plant in high-temperature heat exchangers. The remaining thermal energy in the energy conversion unit is converted into electrical energy in a direct gas turbine cycle. Of the total thermal power of the reactor, which is 600 MW, 160 MW is used for the steam reforming of methane and 435 MW for electricity generation. The design life of the reactor is 60 years.
Another industrial technology for the conversion of natural gas to synthesis gas, partial oxidation (oxidative conversion), was developed in the early 1950s. This is a weakly exothermic process that does not require additional heat input.
СН4 + 0,5О2 <-> СО + 2Н2
ΔН = -44 kJ/mol
As a rule, the process is performed at a pressure of 30-100 atm in a slight excess of pure oxygen compared to the stoichiometry of the reaction in order to provide a more complete conversion and achieve the temperature required for the reaction, which leads to the formation of a certain amount of products of deep oxidation of СО2 and Н2О. The oxidative methane conversion can take place both in the presence of a catalyst and without it. For a non-catalytic process, temperatures of 1200-15000C and a pressure of 2.5-8 MPa are required, at which complete conversion of hydrocarbons is achieved and soot formation is prevented. The thermal efficiency of the process reaches 60-75%. The catalytic process usually uses a nickel or rhodium catalyst, most often using the ZSM-5 zeolites. Herewith, milder conditions are possible (800-9000C, 2.5-3.5 MPa), which allows the technology to be used in low-tonnage processes, and also increases its mobility.
In practice, combined steam-oxygen conversion of methane is often used. In addition to reducing energy consumption, this allows to obtain synthesis gas with a ratio of Н2/СО2, which is the most favourable for the synthesis of methanol and the Fischer-Tropsch products. This process has been successfully implemented at Shell’s Qatar-based Perl GTL, the world’s largest synthesis liquid hydrocarbon production facility. The main disadvantages of the technology for the partial oxidation of natural gas are the large investment in air separation plants, as well as the noticeable formation of soot, which must be removed. There are also problems with the explosion safety of the process.
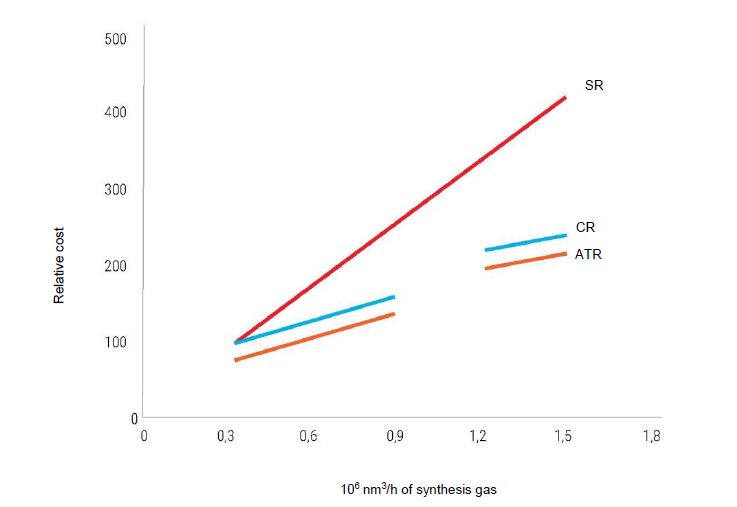
SR – steam reforming; CR – combined reforming; ATR – autothermal reforming [4]
In addition to high temperatures and pressures, in order to achieve a high yield of synthesis gas, it is necessary to ensure a low ratio of О2/СН4 = 0.6–0.7, i.e., to work with very rich mixtures, the ratio of methane and oxygen in which actually lies outside the ignition region for normal conditions, which is extremely difficult. In addition, the commercialization of the partial oxidation of methane is hampered by the large size of the reactors. Shell and Chevron Texaco are the leading developers and licensors of the methane partial oxidation technology.
Autothermal reforming (ATR) is becoming a popular industrial technology for the conversion of natural gas – a combination of an exothermic reaction of homogeneous partial oxidation and an endothermic reaction of steam reforming, the energy for which is obtained due to the partial and complete oxidation of a part of the hydrocarbon feedstock in the same reactor.
The pioneer and most active developer of this process since the 1960s. is the Danish company Haldor Topsoe [3].
The main indicators of various industrial methods for producing synthesis gas are shown in tab. 1 and Fig. 3. With a small capacity of installations (up to 300 thousand m3/h), their relative cost for all processes is approximately the same. With an increase in capacity, the cost of all processes increases linearly, but for steam reforming this growth is noticeably steeper. Therefore, with a capacity of 1.5 mln m3/h, the relative cost of steam reforming is almost twice as high as that of autothermal reforming.
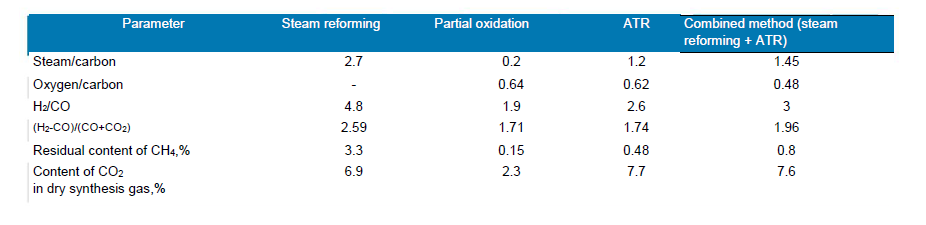
The largest-tonnage product (more than 180 mln t/year) produced on the basis of synthesis gas is ammonia – the basis for the production of nitrogen fertilizers for modern highly productive agriculture. Although ammonia has long been considered as a potential transport fuel [5], as well as a source of hydrogen production [6], serious problems arising in its practical use are still holding back the development of this direction.
The prospects for using for these purposes another product obtained from synthesis gas, methanol, are more obvious. Currently, methanol is a gas chemistry product with the most dynamically growing production volume. There are more than 90 methanol plants in the world with a total installed capacity of about 110 mln t/year. Its world production exceeded 80 mln t/year, and it is projected to reach a level of 120 mln t/year by 2025. The production of methanol is developing especially rapidly in China, which provides almost half of its world production. The volume of methanol production in Russia is 4.4 mln t/year.
Methanol is a versatile product that can replace oil in many petrochemical processes, and a versatile fuel that can be used in almost all types of internal combustion engines (ICE), as well as a fuel for gas turbines and boiler fuel. Finally, methanol is the most convenient liquid carrier for hydrogen. Hydrogen for powering internal combustion engines or fuel cells can be obtained from methanol directly on board a vehicle during its relatively mild steam catalytic conversion.
At the industrial level, the process of converting synthesis gas into liquid synthesis hydrocarbons (Fischer-Tropsch synthesis), which can replace natural oil, has long been mastered [3].
The fractional composition of the resulting products depends mainly on the temperature of the process and the nature of the catalyst used, and is determined by the α coefficient, which reflects the ratio of the growth and termination rate constants of the hydrocarbon chain on the catalyst. It is usually quite wide, from methane to the C50 hydrocarbons and higher (Fig. 4).
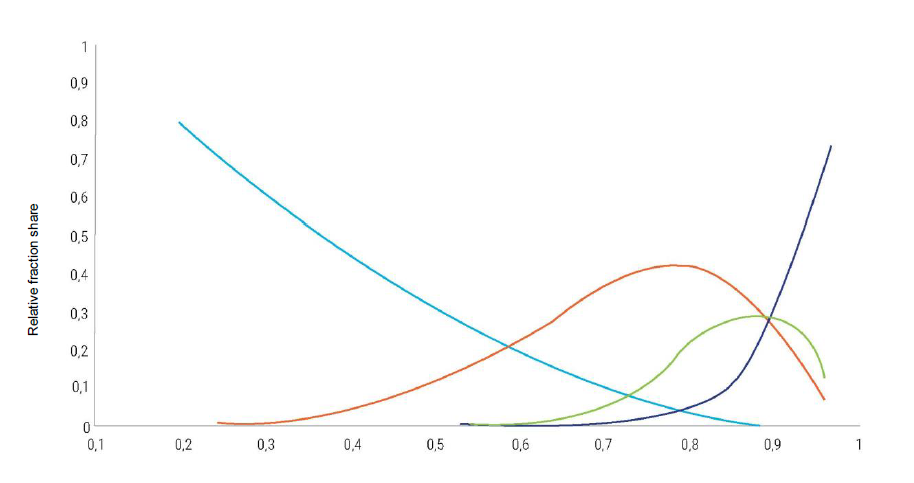
There are several large enterprises in the world for the production of liquid hydrocarbons based on the conversion of natural gas into synthesis gas and subsequent Fischer-Tropsch synthesis, i.e., a scheme called the GTL (Gas to Liquid) technology, with a total capacity of about 10 mln t/year, as well as a number of small pilot plants of various companies. The main GTL products of enterprises implemented on the basis of Shell technology (Perl GTL in Qatar and Bintulu GTL in Malaysia) is diesel fuel. Plants based on Sasol’s GTL technology (Oryx GTL in Qatar, Escravos GTL in Nigeria and others) produce a wider range of products that include, in addition to diesel fuel, gasoline, olefins and oxygenates. In China and South Africa, there are enterprises producing synthesis liquid hydrocarbons according to a similar scheme, but using coal (Coal to Liquid, CTL technologies) as a raw material for producing synthesis gas.
The main problem of modern GTL enterprises is their technological complexity and high costs for the stage of converting natural gas into synthesis gas, which accounts for up to 60% of all costs. Specific capital investments in such enterprises exceed 200 thousand dollars per barrel of daily production, which is several times higher than typical capital investments in oil refineries. Therefore, after the fall in oil prices, the attractiveness of such enterprises fell sharply (Fig. 5), and at present, with oil prices at the level of $ 50–60 per barrel, the construction of new such enterprises is not planned.
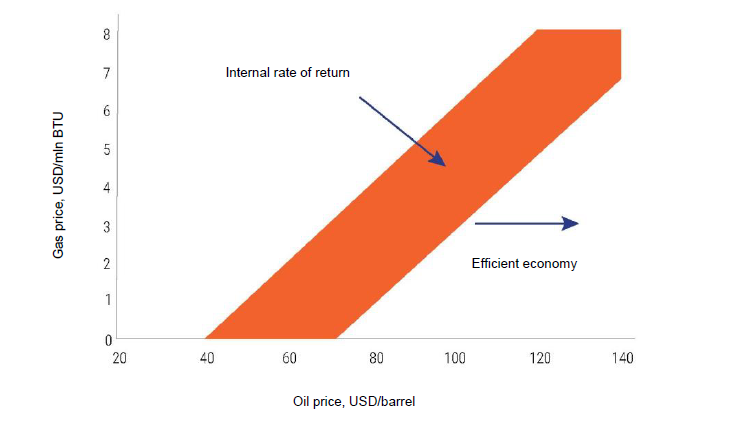
It should be noted that, according to the estimates of VNIIGAZ specialists, when such enterprises are implemented under domestic conditions, specific capex costs will be approximately two times higher than for the conditions of the Mexican or Persian Gulfs.
Alternative technologies for converting methane to synthesis gas
The fundamental disadvantage of modern complex GTL technologies is that they are unsuitable for implementation in medium- and low-tonnage versions, while the overwhelming majority of promising traditional and especially unconventional sources of hydrocarbon gases belong to this category. Therefore, the development of alternative GTL technologies is underway all over the world. The main emphasis is on the creation of simpler and more compact processes for the production of synthesis gas. A number of fundamentally new processes have already been proposed and tested, including processes based on natural gas oxidation on ceramic membranes, processes in microchannel reactors, filtration combustion processes, methane oxidation at millisecond contact times, processes based on energy and electrochemical technologies [3].
So far, none of these technologies have been implemented on an industrial scale, but intensive work is underway in many countries. We will only briefly mention our recently developed matrix conversion method, which allows the process to be performed in an autothermal mode without the use of external heat or energy sources, does not require catalysts, and provides a specific volumetric productivity for synthesis gas an order of magnitude higher than steam reforming. The process allows the use of hydrocarbon gases of almost any composition and origin, and its profitability is weakly dependent on the volume of processed gas [8].
Direct methane to chemical product conversion methods
The high costs of producing synthesis gas stimulate interest in direct processes of converting the main component of natural gas – methane – into chemical products and liquid fuel, which does not require its preliminary conversion into synthesis gas. The most attractive direction remains the oxidative condensation of methane into ethylene – a process that was discovered in the early 1980s and gave rise to the conversion of methane into synthesis gas, then methanol, and then the conversion of methanol to ethylene on zeolite catalysts [3].
Currently, there are several such factories operating in China.
Another method for the direct conversion of methane into chemical products is its partial (partial) oxidation to methanol, which is formed as an intermediate product of incomplete oxidation of methane with a large lack of oxygen. The method was proposed at the beginning of the last century and was used as an industrial one, but due to low conversion high hopes for the creation of effective chemical methods for processing methane. Since ethylene is the basic compound for the production of a large number of products of modern oil and gas chemistry, such a process would completely solve the problem of chemical processing of natural gas. Since then, there have thousands of papers examining it, but it has not yet been possible to achieve the level of commercialization of the process [3]. The economically more profitable process of converting methane into ethylene and further products based on it turned out to be a multistage route with sequential methane per pass and the low selectivity of methanol formation gave way to a process based on synthesis gas. Although recently it has been possible to significantly increase its performance, it remains attractive mainly for low-tonnage processes, for which its simplicity and low capex play a decisive role [3].
APG use in power generation industry
The main reason for the incomplete utilization of APG and its continuing flaring throughout the world is the lack of cost-effective low-tonnage technologies for processing hydrocarbon gases [1, 2], which would make it possible to process APG directly at the production site. Currently, the only break-even way to utilize APG from remote fields, especially in the specific conditions of Russian oil-producing regions, is to generate electricity and heat for their own needs. Up to 30% of the energy of the flared APG could be used to meet the energy demand of the oil fields themselves, which would significantly reduce the volume of the northern delivery of liquid fuel. However, for this, it is necessary to first extract or transform a significant part of methane homologues contained in APG in one way or another. Even an insignificant admixture of heavier alkanes with low octane numbers (RON) and methane numbers (MP) and a high net calorific value 0н makes APG prone to detonation and does not allow reaching the rated power of a gas piston engine (GPE), forcing it to work with a decrease in load (derating) by 20-30% or more, and also leads to its rapid failure as a result of the formation of resinous deposits. And the existing methods of separating heavy components from APG require sophisticated equipment and high energy costs and do not pay off for power plants of small and medium (up to 10-20 MW) power [9].
To convert APG into a conditional gas engine fuel that meets the requirements of manufacturers of small-capacity gas piston power plants, we have developed a method of selective oxidative cracking of methane homologues directly in the APG itself [9, 10]. Oxidative cracking provides 82-85% ethane conversion and almost complete conversion of all heavier hydrocarbons. The total conversion of methane homologues is 92-95%. The main conversion products are ethylene, carbon monoxide, hydrogen and methane. The selective oxycracking method makes it possible to raise the methane number of the mixture by 11-19 points and reduce the net calorific value by 6-8 MJ/m3, bringing both of these indicators to the values recommended by manufacturers for the stable operation of gas piston machines, that is, to obtain fuel gas from APG that satisfies to the requirements of the GRE manufacturers.
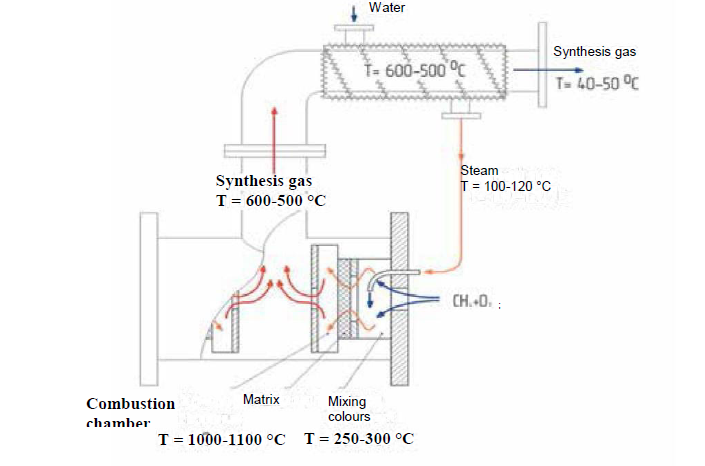
of 30 m3/h of hydrogen-containing gas and [8]
Therefore, it is not surprising that recently the accelerated transition to hydrogen energy has been proclaimed as the main direction of efforts to reduce the “carbon footprint” of the energy sector, that is, the wider use of hydrogen as an energy carrier for energy production, utilities and transport. Russia is actively joining these efforts. By order of the Government of the Russian Federation No. 2634-r dated October 12, 2020, the Action Plan (Roadmap) for the development of hydrogen energy until 2024 was approved.The plan is aimed at increasing production and expanding the scope of hydrogen as an environmentally friendly energy source, as well as joining the country among the world leaders in its
production and export.
The main industrial method for producing hydrogen remains and in the foreseeable future will remain its separation from synthesis gas obtained by steam reforming of natural gas (~ 80% of Н2) and coal (~20% of Н2 production). Renewable sources account for much less than 1% of its world production, and the cost of such hydrogen is at least 3 times higher than that obtained by steam reforming. Therefore, in addition to the issues of storage, transportation and distribution of large volumes of hydrogen, which are still very far from practically acceptable solutions, the fundamental problem of hydrogen energy is to reduce the cost of producing hydrogen, primarily, for the conversion of hydrocarbon gases into synthesis
gas.
Taking into account the unresolved problems of transportation and storage of large volumes of hydrogen, the most reasonable approach, especially for the transport sector, may be its distributed lowtonnage production from network natural gas or easily transported liquid hydrocarbon feedstock
directly at the points of consumption.
The basis for such a distributed production of hydrogen could be the method of matrix conversion of natural gas into synthesis gas [8], on the basis of which the distributed production of methanol, synthesis liquid hydrocarbons, ammonia and other potential alternative energy carriers and liquid sources of hydrogen production can also be organized.
Conclusion
Modern gas chemistry offers a wide range of technologies already mastered by industry and potential technologies for converting hydrocarbon gases of various compositions and origins into more convenient or environmentally acceptable liquid and gaseous energy carriers. However, the economic efficiency of most of these technologies is still insufficient to compete alternative energy sources obtained from natural gas with traditional types of liquid petroleum fuels. Therefore, the most important problem of the transition to such energy sources is the development of the technological
base of gas chemistry.
The work was performed within the framework of the Program of Fundamental Scientific Research of the State Academies of Sciences, topic FIC KhF RAS 0082-2019-0014, state registration number AAAA-A20-120020590084-9 and topic IPCP RAS 0089-2019-0018, state registration
number AAA-A-A19-119022690098 -3.