Svetlana SAIGATKINA
Columnist for Energy Policy
e-mail: gorshkovaaa@minenergo.gov.ru
At the end of April, the merger of the two largest petrochemical companies was announced. As part of the merger, a company will be created on the basis of SIBUR Holding, in which the existing shareholders of TAIF will receive a 15% stake in exchange for the transfer of a controlling stake in a group consisting of petrochemical and energy enterprises. The remaining block of shares in TAIF can be subsequently redeemed by the merged company.
SIBUR is owned by Russian businessmen Leonid Mikhelson, Gennady Timchenko, the SOGAZ insurance company, the Chinese petrochemical giant Sinopec and the Chinese Silk Road Fund, as well as the former and current management.
The shareholder structure of TAIF Group is rather complicated. The decision to create the investment group “TAIF” was made in April 1995 at a meeting with the participation of the President of Tatarstan Mintimer Shaimiev. It was officially known that the son of the former head of the republic Radik Shaimiev owned 11.97% of TAIF, Guzelia Safina – 4.5%, Albert Shigabutdinov, the current head of the TAIF board of directors – 8.02%.
The largest petrochemical assets of TAIF are Nizhnekamskneftekhim (NKNKH) and Kazanorgsintez (KOS). TAIF owns 75.6% of NKNKH, as well as 53.93% of KOS (the structure of the government of Tatarstan owns 19.87% of the authorized capital of KOS).
Moreover, the group includes the generating company JSC TGK-16, as well as the oil complex of TAIF-NK JSC with a network of filling stations. At the end of 2020, the share of TAIF in the total volume of production in the Russian Federation was: for rubbers – 64%, for plastics – 28%, while the group is the only producer of polycarbonates, ultrathene and a number of other popular types of polymer products in Russia.
The deal will be closed subject to the necessary corporate procedures and regulatory approvals.
If it is done, the structure of SIBUR’s owners will look like this: L. Mikhelson (31%), shareholders of TA-IF – 15%, G. Timchenko (14.45%), Sinopec and the Silk Road Fund (8.5% each), SOGAZ (10.625%), acting and former top management (12.325%).
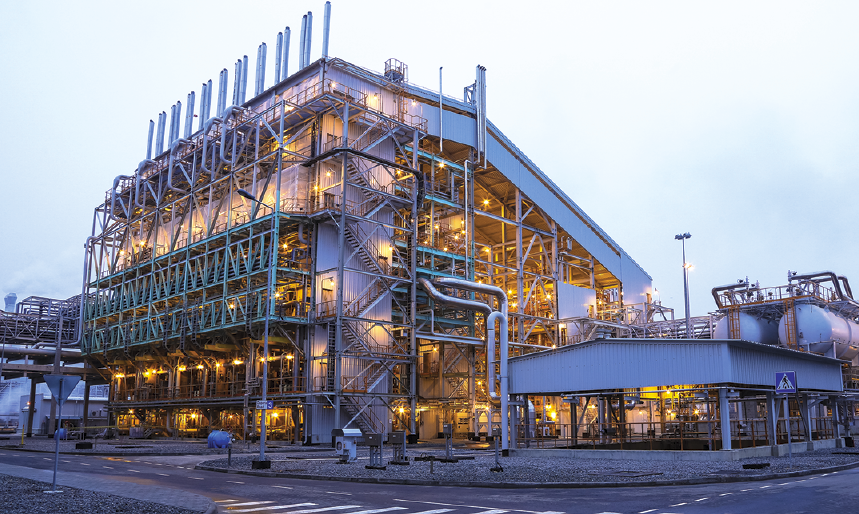
Source: SIBUR
SIBUR
As of the end of 2020, SIBUR has the largest capacities for the production of polyethylene (1.77 mln t) and polypropylene (1.5 mln t). Thus, Zapsibneftekhim (Tobolsk), launched in 2020, can produce 1.5 mln t of polyethylene (low-density polyethylene, linear polyethylene) and 0.5 mln t of polypropylene.
Moreover, the company includes Tobolsk-Polymer, which produces 0.5 mln t of polypropylene, and Tomskneftekhim producing 140 th t of polypropylene and 270 th t of polyethylene. SIBUR’s joint venture with Gazprom Neft – Poliom – produces 218 th t of polypropylene, another joint venture – NPP Neftegazokhimiya – 130 th t.
Rusvinil (SIBUR’s joint venture with Solvay) can produce 330 th t of polyvinyl chloride (PVC) used in the production of pipes and windows, occupying about 40% of the Russian market.
The company’s capacity for the production of polyethylene terephthalate (PET) used for plastic containers is about 300 th t (219 th t are produced by JSC “Polief” in Bashkiria and 75 th t – “SIBUR-PETF” in Tver), while the market share is about 48%.
SIBUR-Khimprom has a production capacity of 100 th t of expandable polystyrene (PSV), and Biaxplen can produce 185 th t of the BOPP films.
As a result, SIBUR is the leader in Russia in the production of low-density polyethylene (LDPE), polypropylene, BOPP films and PSV.
Moreover, Polief is the only Russian producer of terephthalic acid (350 th t), which is required for PET production. SIBUR is also a leader in the production of the second essential component for PET production – monoethylene glycol (MEG). In Russia, apart from SIBUR, this product is produced only by Nizhnekamskneftekhim and Kazanorgsintez, that is, this segment will be monopolized in the event of a merger.
SIBUR also ranks first in terms of capacity for the production of SCS (styrene-butadiene rubber) and DSSK (divinyl-styrene synthetic rubber) – 107 th t and thermoplastic elastomers (TPE) – 85 th t. rubber) – 131 th t.
The main future investment project of SIBUR will be the Amur Gas Chemical Complex (AGKKH) on the resources of ethane and liquefied hydrocarbon gases (LHG), obtained at the Amur gas processing plant of Gazprom. The estimated capacity is 2.3 mln t of polyethylene and 400 th t of polypropylene per year.
In the pandemic year 2020, SIBUR’s revenue due to the variety of goods, the demand for which varied in different directions, decreased only by 1.6% by 2019 – to 523 bln RUR. EBITDA increased by 5% to 179 bln RUR, while EBITDA margin increased by 2.3 pp to 34.3%. Adjusted profit remained at the level of the previous year – RUB 93 bln.
Kazanorgsintez
The exact list of TAIF Group’s assets that will be included in the deal has not yet been announced and will depend, among other things, on the decision of the Federal Antimonopoly Service (FAS). The department already emphasizes that due to the scale of the transaction, it is necessary to assess its impact on both the domestic and foreign markets for the production and processing of petrochemicals.
In the event of the merger, SIBUR will absorb its two closest competitors in the production of polyolefins (polyethylene and polypropylene) – Kazanorgsintez is the second largest producer of polyethylene – 727 th t, NKNKH can produce 210 th t of polyethylene and the same amount of polypropylene.
KOS produces over 170 brands of chemical products – polyethylene, bisphenol A, polycarbonate, polyethylene pipes, ethylene glycols. The total annual production is 1.7 mln t.
KOS is still the only one in the country using ethane supplied by pipeline from the Orenburg gas processing plant of Gazprom, as well as the Minnibaevsky gas processing plant of Tatneft. Previously, KOS had frictions with Gazprom over the supply of ethane, but after lengthy negotiations, a long-term contract was signed.
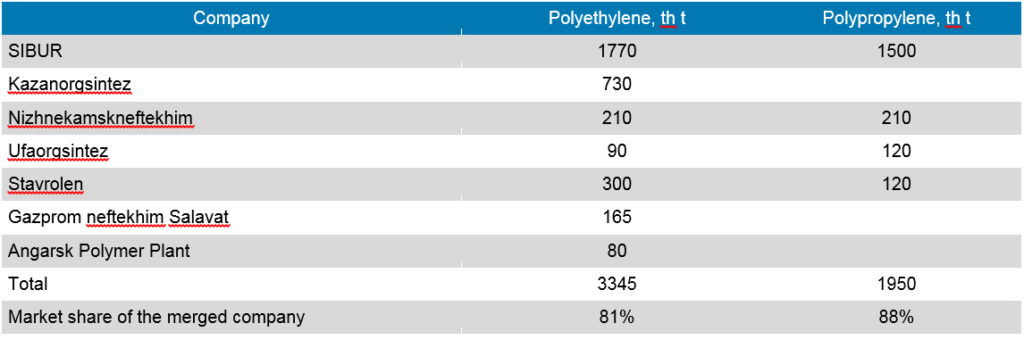
Currently, the enterprise is implementing a project to modernize its ethylene production in order to compensate for the ethane deficit by organizing the technical feasibility of processing an alternative feedstock – propane, as well as increasing the volume of ethylene production. The main types of raw materials for Kazanorgsintez are ethane, ethylene, propane-butane and benzene; from time to time the company buys commercial ethylene from NKNKH.
By the end of 2020, SIBUR sold 3.3 mln t of LHG to third-party companies, which was 35% less than a year earlier, as it began to involve LHG in the oil and gas chemistry at Zapsibneftekhim. Thus, SIBUR can become a supplier of LHG for the enterprises of Tatarstan.
KOS produces 100% domestic polycarbonate, bisphenol A and ultrathene.
Herewith, the bulk of the produced bisphenol A is directed to the production of polycarbonate, and bisphenol A is also used in the production of epoxy resins used in various industries. Polycarbonates are widely used as structural materials in the automotive industry, electronic and electrical industries, household and medical equipment, instrument and aircraft manufacturing, industrial and civil construction. Polycarbonate sheets are used for glazing buildings and sports facilities, greenhouses and for the production of high-strength laminated glass.
In the market of manufacturers of polyethylene pipes KOS has a 25% share, being one of the three leading in Russia. The pipes produced are widely used in gas supply systems, water supply systems, sewerage systems, and process pipeline systems.
In 2020, KOS’s revenue amounted to about 62.8 bln RUR, of which the largest share were polymers and copolymers of ethylene – 70% and polycarbonates – 16%. KOS’s net profit in 2018 is 19.9 bln RUR, in 2019 – 11.6 bln RUR, in 2020 – 8.6 bln RUR.
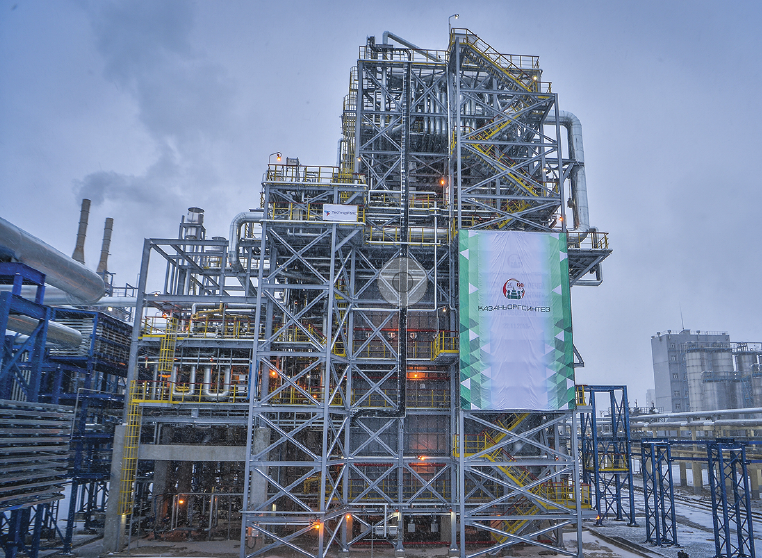
Source: vremiarossiii.rf
Nizhnekamskneftekhim
Nizhnekamskneftekhim (NKNKH) closes the top three in terms of ethylene capacity in Russia – 600 th t/year, ranking first in the sector of synthetic rubbers (SR). The total capacity of the company for the production of base polymers is 680 th t/year.
The company is the world leader in the production of isoprene rubber with a 37.8% share in the global market and the third largest supplier of butyl rubbers in the world with a 16.3% share. Moreover, NKNKH occupies 4.7% of the global butadiene rubber market, being one of the TOP-10 world producers of synthetic rubber.
NKNK is building a new complex for the production of ethylene with a capacity of 600 th t/year, as well as its derivatives, including polyethylene and polypropylene. Moreover, the capacity of isoprene production is being increased up to 333 th t/year, the capacity of halobutyl rubber (GBR) is planned to be increased from 150 to 200 th t/year.
The share of NKNKH’s synthetic rubber sales to Europe is 35.4%, to Asia – 31.3%, the North American market accounts for 10.7%, and to Russia – only 8.6%. Herewith, NKNKH sells almost all plastics on the domestic market – 83.6%, another 11.9% falls on the markets of neighbouring countries, and only 3.6% in Europe.
In addition to rubbers and plastics, NKNKH also produces and sells other petrochemical products based on olefins and their derivatives – polyesters, glycols and glycol ethers, propylene trimers and tetramers, surfactants and other types of products. For a number of them, Nizhnekamskneftekhim is a significant participant in the Russian market.
In particular, the company is the only domestic large-scale producer of polyether materials based on propylene oxide, the only producer of propylene trimers and tetramers, non-ionic surfactants (surfactants) based on alkylphenols in Russia and neighbouring countries, and the second largest Russian supplier of ethylene oxide and ethylene glycols.
By 2025, NKNKH expects to produce 1.2 mln t of ethylene, 0.8 mln t of rubber and up to 1.4 mln t of plastics.
New company
After the completion of all investment projects that are underway, the merged SIBUR will enter the TOP-5 global leaders in the production of polyolefins (polyethylene and polypropylene) and rubbers, the partners expect.
Currently, the largest companies for the production of polyethylene and polypropylene in the world are ExxonMobil, Dow Chemical, SABIC (Saudi Arabia), the shareholder of SIBUR is the Chinese Sinopec, LyondellBasell Industries, Ineos, BASF, Braskem, Borealis, etc.
As a result, the merged company will occupy 81% of the Russian market for polyethylene (various grades), and 88% for polypropylene.
Other producers of polyethylene and polypropylene in Russia are Ufaorgsintez (part of Rosneft), Stavrolen (LUKOIL), Angarsk Polymer Plant (Rosneft), Gazprom neftekhim Salavat.
Industry state
The global consumption of basic polymers in the world in 2019 (data from IHS Markit, cited by SIBUR) amounted to 250 mln t, of which the largest was polyethylene – 105 mln t or 42%, polypropylene accounted for 76 mln t (30%), demand for polyethylene terephthalate (PET) amounted to 10% – about 25 mln t, the rest of polyvinyl chloride (PVC) – 18% or 45 mln t. Demand for polymers since 2017 increased by 18 mln t, polyethylene consumption increased by 8 mln t, and polypropylene – by 6 mln t, the distribution of shares did not change.
According to IHS calculations, during 2015-2019, the average annual growth rate for polypropylene was 4.7%, for polyethylene – 4.3%, while in Asia these indicators were 6.3% and 7.4%, respectively. Herewith, the average annual growth rate of the world gross domestic product (GDP) was only 2.9%.
The petrochemical industry is cyclical, and after a period of recovery in 2015-2018, the slowdown in economic growth in countries like China has had its negative impact – the demand for many petrochemical products began to fall along with prices.
Herewith, production was launched, the decision to invest in which was made in the “fat” years, which created a situation of overheating.
In particular, thanks to the shale revolution and, accordingly, the emergence of cheap ethane, the United States boomed in the production of ethylene and its derivatives – in 2015-2019, unprecedented volumes of capacity for ethylene, one of the main links of the petrochemical chain, were built in North America.
Today, the total capacity of ethylene production complexes in the world is about 175 mln t, the USA is the leader here – 36 mln t, followed by China – 20 mln t, Saudi Arabia – 18 mln t.
According to Andrey Kostin, Director General of the Centre for Industrial Research, petrochemicals are now in a phase of global decline. “Due to the previous successful years, a lot of capacities have appeared, which puts pressure on prices, as a result, the utilisation of these capacities around the world decreases, and people lose interest in investments, while demand continues to grow. At some point, the utilisation of current capacities will reach high levels, prices will start to rise and investments will resume again. The next growth will start in about 4-6 years, so now is the time to start building so that capacity will enter the market in the growth phase,” he said.
The IHS experts believe that during 2020-2024, with the growth of world GDP by 3.8% each year, the consumption of polypropylene in the world will grow by 4.7% per year or by 4 mln t, and polyethylene – by 4.3% or 5 mln t/year. For Asia, these figures will be even higher – 5.9% and 5.7%, respectively.
“The global petrochemical industry is among the most dynamically developing ones, significantly outstripping world GDP in terms of growth rates (4 and 2.5% per year on average over the past 10 years, respectively).
Herewith, it is very resistant to changes in the global economic environment – so, even considering the coronavirus pandemic, the implementation of quarantine restrictions and the closure of borders, some segments of petrochemicals (in particular polymers) in 2020 showed a positive trend in consumption”, says Artem Lebedskoy-Tambiev, the VYGON Consulting specialist,
“In the future, the trend will continue, and the main contribution to the growth in demand will be made by the developing countries of the Asia-Pacific region (APR), Africa and the Middle East. Currently, most of the petrochemical capacities are processing naphtha, but its share will decrease with the implementation of new pyrolysis on ethane and LHG in regions with cheap raw materials (the Middle East, Russia and the USA),” he believes.
Russia’s plans
It is extremely difficult to consider petrochemical capacities and their development, due to the wide range of raw materials and manufactured products. One of the options is to consider the pyrolysis capacities for ethylene as the main product. Ethylene derivatives can be polyethylene, ethylene oxide, styrene and other products, which, accordingly, can be converted in plastics.
Thus, pursuant to the calculations of the Ministry of Energy, ethylene production in Russia in 5 years may increase threefold – from 4.77 mln t to 12.4 mln t/year, and by 2030 – up to 15.14 mln t/year.
If the announced plans of all Russian companies are implemented, the share of the merged SIBUR in ethylene production may decrease to 48% by 2025 compared to the current 63%.
Currently, Russian facilities are represented as follows: 1.5 mln t of ZapSibNeftekhim, 600 th t of Nizhnekamskneftekhim, 640 th t of Kazanorgsintez (MOEX: KZOS), 300 th t are produced by the Angarsk Polymer Plant, 420 th t by SIBUR-Kstovo, other producers – 1.31 mln t.
Ethylene production capacities by 2025 are planned to be commissioned not only by SIBUR (2.3 mln t at the Amur Gas Chemical Complex) and Nizhnekamskneftekhim (+600 th t). The main growth is expected to come from Ruskhimalliance (a joint venture of Gazprom and RusGazDobycha), which plans to launch a capacity of 3.1 mln t of ethylene.
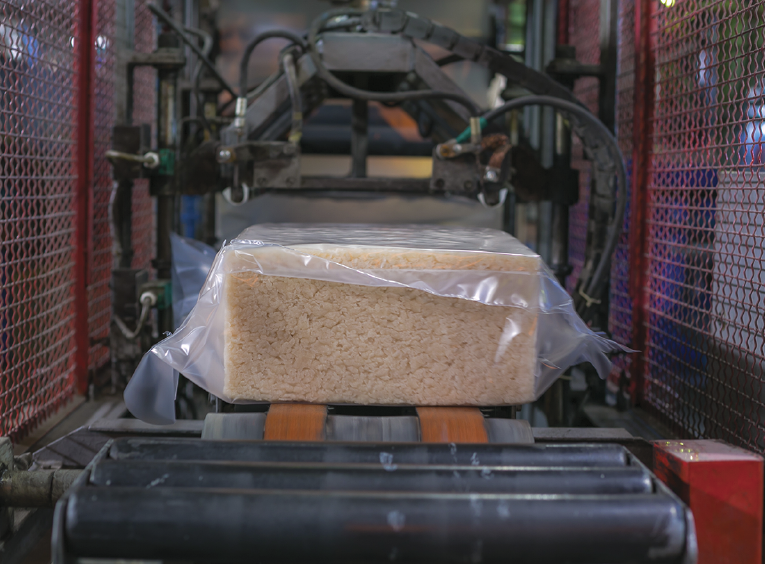
Source: SIBUR
The Irkutsk Oil Company (INK) is building the Irkutsk Polymer Plant, which will produce 670 th t of ethylene per year. Gazprom is not giving up with the construction of the Novourengoy gas chemical complex for 420 th t/year. Other producers are expected to increase ethylene production from 1.3 mln t/year in 2020 to 1.8 mln t/year in 2025 and up to 1.96 mln t/year in 2030: In 2030, LUKOIL plans to launch pyrolysis at 1.1 mln t/year, Vostochnaya NHK – 1.43 mln t, and the Angarsk Polymer Plant will increase its capacity from 300 to 454 th t/year.
According to the calculations of the Ministry of Energy, having implemented these plans, Russia will take 6.3% of the global ethylene market, compared with the current 2.7%.
According to A. Lebedskoy-Tambiev, considering the plants for the production of propylene, the total capacity of olefins production in the Russian Federation is about 8.5 mln t and does not exceed 3% of the world scope.
To implement plans for the development of petrochemicals, the RF Government has taken measures to stimulate the involvement of gas raw materials in petrochemicals – ethane and liquefied hydrocarbon gases (LHG). For them, a reverse excise tax was introduced if they were involved in the creation of petrochemical products. The reverse excise tax on naphtha has been in effect for several years.
“Since the reverse excise tax has been applied to all petrochemicals operating on naphtha for several years, the decision to introduce a reverse excise tax on ethane and LHG actually levels the playing field for chemical production using various raw materials. Moreover, in order to take advantage of the privilege, petrochemical enterprises will need from January 1, 2022 either to launch additional processing capacities in the amount of at least 300 th t/year, or to carry out a significant modernisation of the existing production,” A. Lebedskoy-Tambiev noted.
“The yield of olefins from naphtha pyrolysis is lower than that from pyrolysis on
light feedstock, therefore, a paradoxical situation developed, in which production was maintained less efficient in terms of polyolefin production (a key and until recently scarce product).
Moreover, due to infrastructural constraints, ethane processing in Russia is practically undeveloped – out of 10-12 mln t of ethane, which is contained in the produced natural gas, only about 700 th t are processed. Therefore, the implementation of incentive support will increase the economic efficiency of complex production these projects are profitable,” he believes.
According to the Ministry of Energy, in general, as a result of measures to support the petrochemical industry, its production will grow by 8-16 mln t, the additional investment funds in the amount of 2.6-4.6 trln RUR will be attracted to the industry until 2030, non-resource exports will grow by USD 9-18 bln.
“Each ton of raw materials – naphtha, LHG, ethane – gives an increase in added value up to four times relative to the basic raw material. This is much higher than the added value of refining”, said Alexander Novak, the RF Deputy Prime Minister.
According to him, over the past seven years, the production of large-scale polymers and synthetic rubbers in Russia at the end of 2019 increased by almost 50% and reached 6.8 mln t. Zapsibneftekhim entered the world’s top ten ethylene production capacities, and will be the largest in the world in terms of the volume of LHG processing.
“Until recently, the key market for domestic petrochemical producers was the domestic market, the only exception being rubbers, over 70% of which is exported. Due to the fact that Zapsibneftekhim reaches full capacity, the needs of the Russian market for base polymers from 2020 will be fully covered by domestic producers. Therefore, the majority of large-scale projects planned and under construction in Russia (with a total capacity of over 9 mln t) are export-oriented”, A. Lebedskoy-Tambiev said.
The rubber industry is in a much more difficult situation than polymers, and not for the first year, and in the pandemic it got even more. According to the International Rubber Study Group, global demand for rubbers fell 1% in 2019 and 6.5% in 2020.
Rubber production fell 1.1% in 2019 and 4.9% in 2020. In 2019, the production of rubbers in the world, both natural and synthetic, amounted to about 29 mln t (1.1% less than in 2018), and in 2020 fell by 4.9% to 27.7 mln t. Thus, Russia, having produced about 1.5 mln t of rubber in 2020, occupies about 5% of the world market. Europe produces about 4 mln t of synthetic rubber, Africa – 1.1 mln t of natural rubber, America produces 2.75 mln t of synthetic rubbers and 340 th t of natural rubber, Asia – 12.3 mln t of natural and 8.4 mln t of synthetic rubber.
The Vygon Consulting expert noted that the competitive advantages of the Russian petrochemical industry are “large volumes of cheap raw materials, the low cost of which is ensured by tax and customs subsidies, as well as the cost of their transportation.”
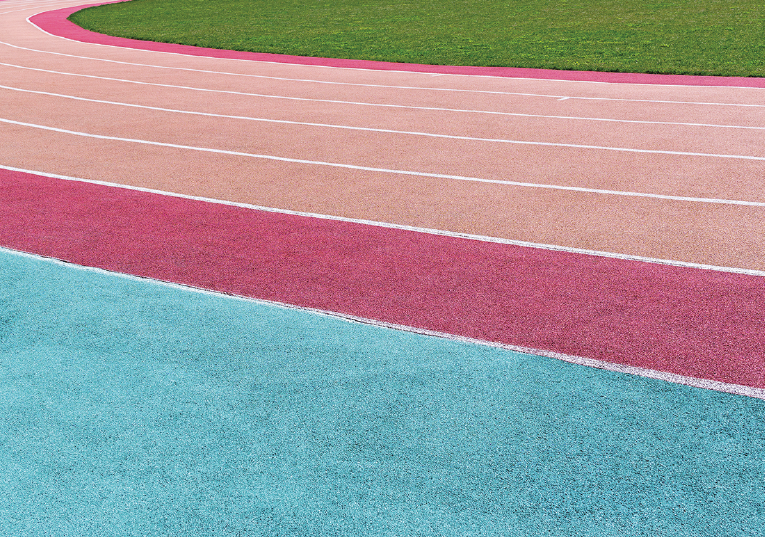
Source: HannaAlandi/Depositphotos.com
Place in the world
Despite the fact that the main projects under construction are still export-oriented, Russia also intends to develop the domestic market for the consumption of petrochemical products.
The idea to combine the petrochemical businesses of TAIF Group and SIBUR, as L. Mikhelson said, was born ten years ago. He suggested that these intentions were prompted by a meeting with Russian President Vladimir Putin on the development of petrochemical industry in Tobolsk.
At that meeting, the issues of increasing demand for petrochemical products, as well as new measures to support the industry, were discussed in detail.
The pandemic year brought uneven results for the oil and gas chemical industry, due to the variety of products it produces. Since humanity has been quarantined in homes, the use of plastics in industries such as the automotive industry has dropped, and for the same reason the production of rubber for tires has dropped. But on the other hand, people required more computer equipment and various gadgets that also use plastics.
While people were locked in their old houses, construction companies continued to build new ones with the support of the government – they required polymer pipes, PVC plastic windows, insulation, and much more. But the most serious locomotive, of course, has become medicine – it is from polypropylene that medical masks and protective clothing are made. There is a strong demand for disposable packaging. Herewith, methanol, which is used for the production of motor fuels, was seriously affected.
So far, experts do not undertake to predict how long these new trends will be, in particular, how much the ability to work remotely will affect the consumption of various types of plastics.
“Demand for expensive durables like cars will depend on consumer confidence and how quickly labour markets recover. Although many governments are introducing stimulus measures, recovering to dock levels will likely take several years for many chemicals. It is also likely that there will be long-term changes that we do not yet know about.“Work from home” has proven to be efficient for many companies and will impact the automotive, building construction and fuel markets,” said Chuck Carr, Vice President for aromatic hydrocarbons and refining and petrochemical integration at IHS Markit.
During the meeting, the head of SIBUR Dmitry Konov, despite the fact that the largest producer of rubbers is NKNKH, asked for the entire industry: “Key quotations for rubbers – both natural and rubber related to the tire industry – have been steadily declining over the past 10 years.”
According to him, due to the subsidence of the automotive industry against the background of the pandemic and other factors, “many types of rubber are really on the verge of operating profitability.”
As a result, the government is now looking for ways to support synthetic rubber producers – again considering the implementation of a reverse excise with a damper mechanism.
Moreover, at the request of Igor Sechin, the head of Rosneft, the issue of supporting the construction of VNHK (Eastern Petrochemical Company) is being considered, and at the request of LUKOIL President Vagit Alekperov – a proposal to stimulate the involvement of propylene produced at oil refineries in the petrochemical process.
Measures to stimulate polymer consumption are being explored as well. “Currently, the consumption of polyolefins in the Russian Federation is about 3 mln t, while in terms of growth rates Russia has historically lagged behind world indicators. It should be noted, however, that the domestic market has the potential for significant growth. Consumption of plastic per person in Russia is more than 2 times less than in Europe. Therefore, the development of consumer industries, primarily construction and packaging production, will also become a driver of growth and chemistry”, says A. Lebedskoy-Tambiev.
According to IHS Markit and the IMF, provided by SIBUR, the consumption of polyethylene per capita in Russia amounted to 13.4 kg per person in 2019, slightly more than in the main consumer of petrochemical products – Asia, while in Europe – about 26 kg per person. person, and in North America – 33 kg per capita.
D. Konov drew the attention of the President of the Russian Federation to the fact that in Russia, in comparison with other countries, the use of polymer solutions that save money during the construction phase and especially during the operation phase is significantly lower than in Europe.
As a result, the government was instructed, when developing an action plan for the modernisation of communal infrastructure facilities (heat supply facilities, water supply and sewerage systems), the wear rate of which exceeds 60%, to provide for “the use of innovative materials of domestic production that ensure the energy efficiency of communal infrastructure systems”. It was also instructed to consider the issue of expanding the use of polymeric materials in oil and gas production and the construction of oil pipelines.
Fly in the ointment
SIBUR understands that the disadvantages of polymers in the society’s environmental agenda, which has come to the fore, are their “visibility”. Waste plastic pollutes both the soil and the world’s oceans, decomposing for decades and poisoning the life of living organisms.
“We will work to recycle plastics,” promised D. Konov.
In turn, V. Putin stressed that petrochemical plants play an important role in the climate agenda of our country – to reduce the share of flared associated petroleum gas, the main processor of which is SIBUR. The President noted that in the production of plastics, carbon dioxide emissions per ton of products are 13 times less than in the production of other materials: aluminium, copper, steel and iron.
According to A. Lebedskoy-Tambiev, the main source of greenhouse gases in the production of petrochemical products is pyrolysis, and at the moment the total emissions are about 7.6 mln t of CO2. “It is worth noting that, due to the active commissioning of new capacities, a significant increase in greenhouse gas emissions is expected in the future – by 2030 by more than 2.5 times,” he said.
“Today, greenhouse gas emissions from new pyrolysis in Russia and abroad are almost the same, while emissions during the transport of bulk cargo, such as polymers, are significantly lower than when transporting gaseous or compressed raw materials (ethane and LHG). Therefore, from the point of view of the carbon footprint, it is more efficient to build petrochemical facilities at the place of production of raw materials,” the expert summed up.
On behalf of the President, the Government of the Russian Federation shall develop a set of tax and other incentive measures aimed at ensuring by 2030 the production of 25% of finished products from polyethylene terephthalate and 10% of finished products from polyolefins with the obligatory use of secondary raw materials from polymer waste and (or) materials containing such raw materials, and ensure the implementation of these measures.
By the end of June, the Government of the Russian Federation shall update the action plan for the development of the petrochemical complex of Russia for the period up to 2025.