Denis KHITRYKH
PhD, MBA, Director of Research and Development
Center, Marketing Director, CADFEM CIS
e-mail: denis.khitrykh@cadfem-cis.ru
Introduction
The move to Industry 4.0 implies the ability of companies to integrate digital and physical technologies to improve operations and increase productivity. This requires profound changes in production and business processes.
For industrial enterprises, digitalization means both the integration of production processes within the enterprise, and the integration of related and dependent enterprises into value chains, at all stages of the product life cycle, from development and production to after-sales service and disposal.
The main goal of digital transformation in the oil and gas and oil refining sectors is to platform business processes, taking into account the characteristics of these industries. This involves the digital transformation of two main processes: production and organizational business models through the use of modern technology.
Unfortunately, the oil industry is quite conservative and the least subject to change. Therefore, currently we can talk about a rather low activity in the implementation of digital technologies in this area. However, it is digitalization that can significantly increase the competitiveness of enterprises in this industry, in particular, oil refineries.
One of the strategic directions for the development of all oil refineries in Russia is to improve the reliability, safety, energy efficiency and environmental friendliness of the equipment being operated. Domestic and foreign experience of refinery operation shows that damage or failure of the pumping equipment of the refinery can lead to significant material damage and even death of workers. To ensure the safe operation of refinery equipment, it is necessary to ensure a high probability of reducing emergency situations. In addition, despite the relatively low cost of pumping equipment, the daily downtime of one technological unit, for example, a distillation column, due to the unreliable operation of the main and auxiliary pumps, can entail millions in losses.
Today, at each refinery in the CIS countries, on average, up to 3000 units of pumping and compressor equipment with a capacity of up to 1200 kW are in operation, which consume up to 80–90% of the total electricity volume. Herewith, the age of 20–30% of the pumps exceeds 30 years, and the majority of equipment failures occurs precisely because of its unsatisfactory technical condition [4].
Therefore, most of the country’s oil refining companies are aware of the need and importance of introducing intelligent means of monitoring the technical condition of pumping systems, and the transition from the system of scheduled preventive maintenance to the system of repairs based on the actual state [1].
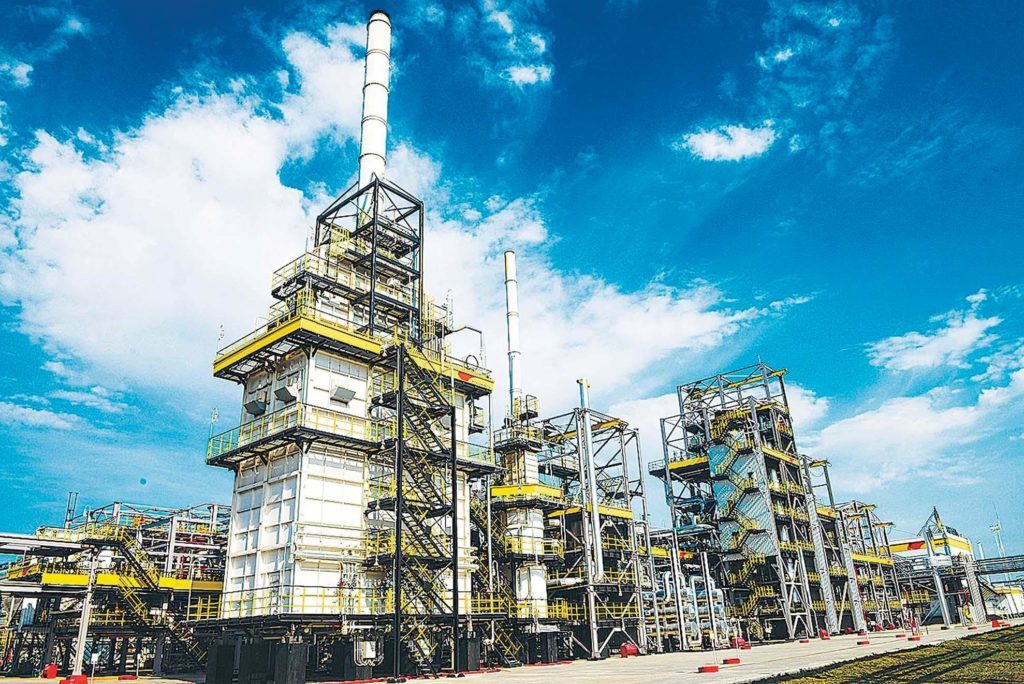
According to the data of works [2] and [3], the implementation of repairs based on the actual technical condition can bring benefits to the enterprise in the amount of 30% of the total cost of the equipment in operation, and the digital twin of the equipment is a key element of the strategy for the implementation of maintenance and repairs based on the actual condition at oil refineries.
There are examples of successful implementation of digital twins of pumping units of different levels in the world. However, there is still no accurate assessment of the efficiency and cost of introducing digital twins of refinery pumping systems in the open press.
Russian oil refining industry at the current stage of development
The efficiency of the oil refining industry as a whole follows the trend of the country’s main macroeconomic indicators and depends on changes in consumer demand. The action of the damping mechanism in the context of a sharp drop in prices for oil products in 2020 on world markets led to the fact that the domestic market became a premium for oil companies, but as a result, they were forced to pay a reverse excise tax on oil to the budget. Thus, in the context of a pandemic, two strategic state tasks were solved: budget filling and maintaining fuel prices with a sharp decline in oil prices. However, the same mechanism led to a drop in the profitability of oil refining.
Data from open sources allow to assess the technical condition of the Russia’s oil refining industry. Thus, according to the information of the Ministry of Energy of Russia (register of refineries), out of 38 large refineries with processing volumes of more than 1 mln t/year, 24 refineries have been operating for more than half a century. The most indicative in this context are the following refineries:
– Tuapse, operating since 1928;
– Saratov, operating since 1934;
– Moscow, operating since 1938.
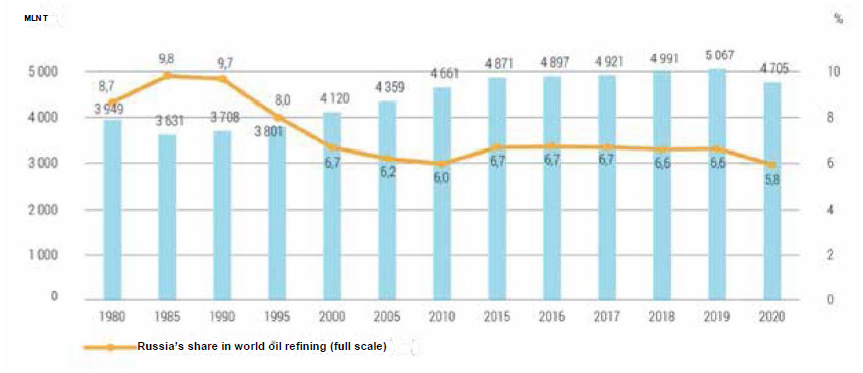
The average age of Russian refineries is over 60 years. This indicates the deterioration of oil refining facilities.
Herewith, in 2019–2020 the largest oil refineries in Russia continued the reconstruction and commissioning of new technological facilities within the framework of the national modernization program. In particular, this program is aimed to increase the production of high-octane gasolines compliant with the Euro-5 and higher standards. As a result, according to [6], the average depth of oil refining at Russian refineries over the past 5 years has grown by 17% and in 2020 amounted to 84.4%.
Oil supplies for refining in the Russian Federation in 2020 amounted to 275 mln t, which is 5.2% lower than in 2019 and corresponds to the level of 2013.
The reduction in the volume of primary oil refining in Russia occurred in two waves: in 2015–2017. and 2019–2020. According to the FEC CDD, the volume of oil refining in Russia in 2020 decreased by 5.4% compared to 2019 and amounted to 270 mln t.
All changes in the industry over the past 5 years are associated with legislative decisions in the field of taxation, a decrease in the attractiveness of the export of dark oil products, pressure on oil consumption, fuel efficiency in the transport sector, regulation of the domestic fuel market with a reduction in production under the OPEC+ deal and a decrease in the profitability of oil refining due to the coronavirus pandemic.
Thus, the tax manoeuvre that ended in 2018 led to a significant reduction in fuel oil production. In the structure of production of basic petroleum products, its share decreased by half; some of the independent and simplest refineries ceased their activities, while the share of complex refineries increased. Over the entire period of the tax manoeuvre, the losses of refineries that do not meet the criterion for deliveries to the domestic market or have not concluded modernization agreements exceeded 50 bln RUR.
In April 2020, OPEC+ parties, including Russia, struck a new deal to cut oil production following a sharp drop in oil demand due to the coronavirus pandemic. According to [5], the parameters of the new OPEC+ agreement envisage three stages of reducing oil production:
– Stage 1: from May to June 2020 – reduction of production by 9.7 mln bbls/day compared to the baseline;
– Stage 2: from July to December 2020 – reduction of production by 7.7 mln bbls/day compared to the baseline;
– Stage 3: from January 2021 to April 2022 – production reduction by 5.8 mln bbls/day compared to the baseline. The production level in October 2018 was taken as the baseline. For Russia, the baseline is set at 11 mln bbls/day. Another of the key problems of the Russian oil refining industry is its strong dependence on imported technologies and equipment. Currently, the industry does not have strict bans on the use of imported equipment, which slows down the process of import substitution.
Flowserve Hybrid Digital Twin Concept
In 2016, PTC, Flowserve, National Instruments and Ansys presented to the engineering community a prototype of a hybrid digital twin, created on the basis of numerical calculations and using a surrogate model of pumping unit behaviour [7]. Three years later, Grundfos created a similar digital twin of the pump, but on a different IoT platform.
A Flowserve Durco Mark 3 overhung centrifugal pump equipped with a basic vibration monitoring system, pressure transducers and a flow meter was selected for the pilot project of the digital pump twin. PTC’s ThingWorx IoT platform was used to integrate all devices, sensors and data analysis. The machine learning subsystem built into ThingWorx was used to analyse information from sensors, build data templates typical of normal pump operation, identify anomalies, find patterns and predictions, and visualize data.
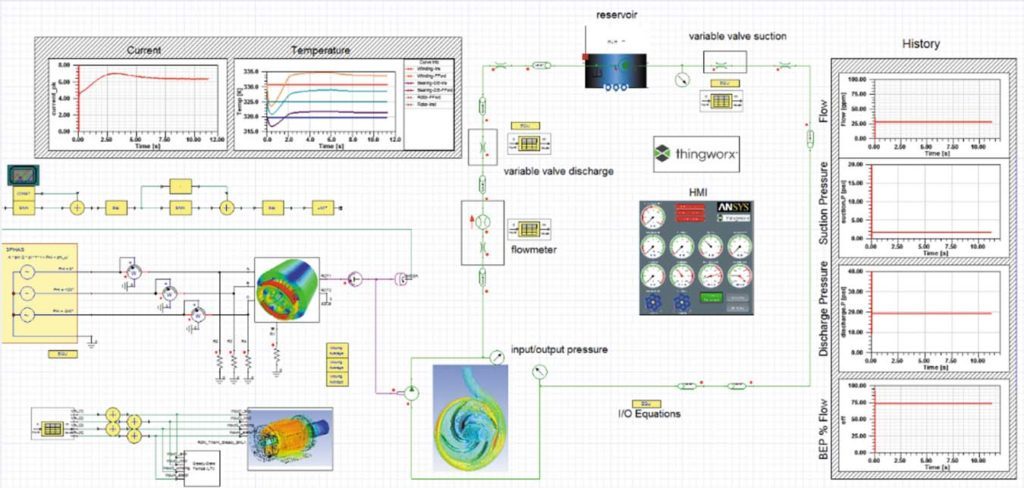
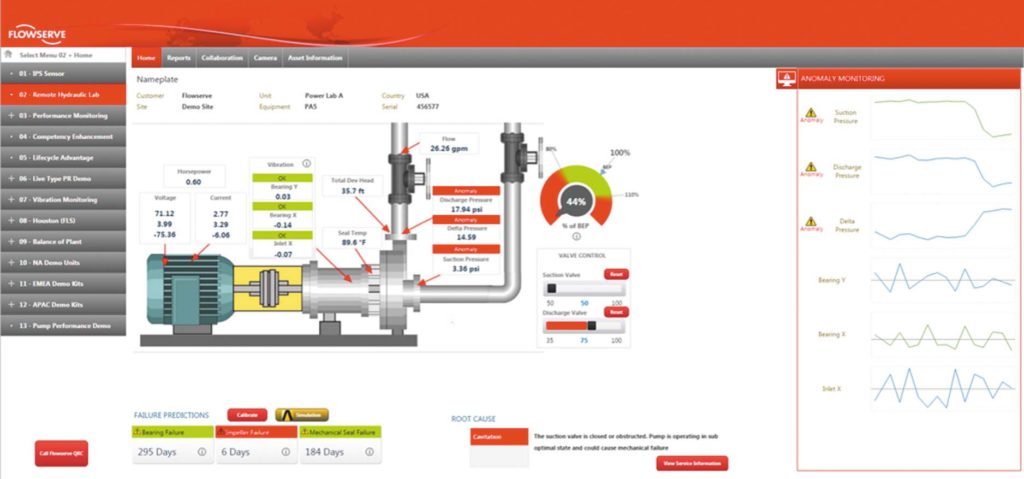
ENERGY
In 2019, the Russian company KAD-FEM CIS developed its own demonstrator of the digital twin of a overhung centrifugal pump – the first example in Russia of implementing the concept of a hybrid digital twin at an industrial level.
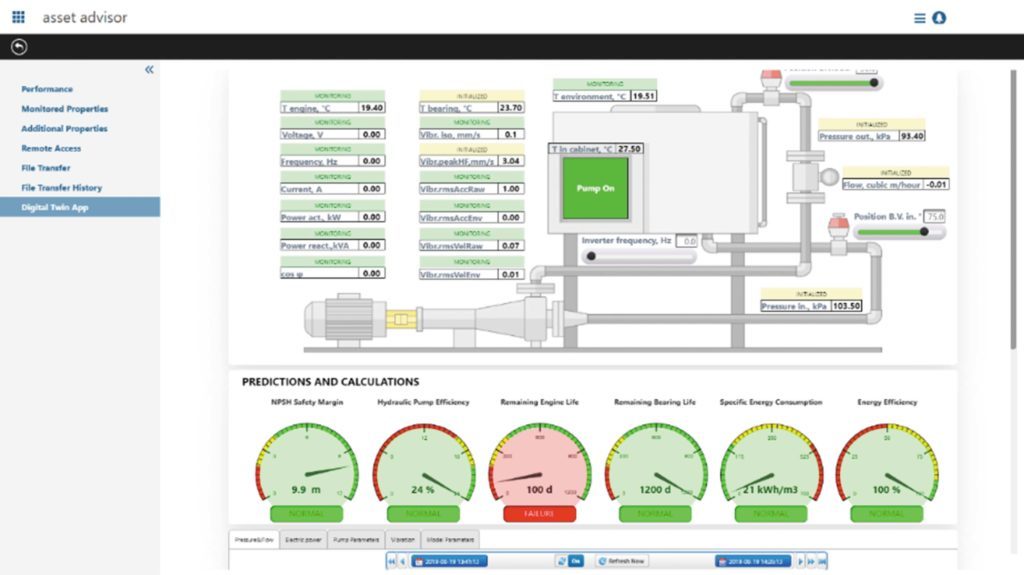
The following functions of the hybrid digital twin have been implemented in the demonstrator:
1. Virtual sensors of the reference process, duplicating the readings of physical sensors.
2. Analytical calculation of the hydraulic characteristics of the pump based on the data of the system model – hydraulic ER and pump cavitation reserve.
3. Calculation of indicators of energy efficiency of the pumping unit.
4. Predicting the residual life of critical pump and motor parts based on regression methods to predict failures based on direct measurements of equipment operation parameters.
A user interface, shown in Fig. 4, was developed to interact with the operator.
Economic effect from the introduction of a digital twin of the refinery pumping unit
The economic effect from the introduction of a system of intelligent (smart) and continuous diagnostics of the technical condition and regulation of the operating mode of the pumping unit based on the digital twin consists of direct and indirect savings. Direct savings include: reduction in repair costs; increase in the overhaul period due to unreasonable scheduled repairs; minimization of the amount of repair work; saving of consumed electricity (due to regulation of the operating mode of the pumping unit). Indirect savings are added by reducing costs not related to production costs: losses resulting from unplanned downtime, for example, losses in the form of unearned income (lost profits) for the shipment of petroleum products and the cost of correcting accidents.
Let us consider the efficiency of using a digital twin based on vibration monitoring and machine analytics using the example of a circulating reflux pump used in a vacuum distillation column of the digital twins for all such refinery equipment, the economic effect will be several orders of magnitude greater. The payback period of the event when only a vibration analyser is employed at a cost of 1.5 mln RUR will be a month and a half.
Calculation of the economic efficiency of the development of a digital twin pump for a refinery
To calculate the economic efficiency of the project implementation of the hybrid digital twin of the pumping unit, it is necessary to assess the possible duration of the project, as well as its cost.
The pump repair costs are estimated by LUKOIL-INFORM at 12,000 USD, loss of profit is 15,000 USD/h, and the total lost profit amounts to 90,000 USD, while the total cost of failure is 158,000 USD.
Thus, losses from equipment downtime in monetary terms in the absence of timely vibration diagnostics and predictive analytics of the circulation pump amount to 11,850 thousand RUR/year with two unscheduled shutdowns. If we scale the effect of implementation It is impossible to estimate the duration of the project implementation by the method of comparison/comparison with similar projects due to their absence in Russia. When calculating the cost of the project, it is necessary to consider both the cost of attracting contractors and the refinery’s own expenses. Taking into account these facts, we can assume the approximate labour costs for the implementation of the digital twin project.
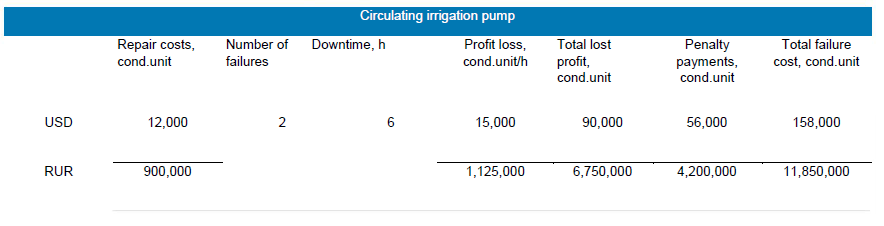
A team of 10 technicians will be more than enough to carry out a digital twin pilot project. The duration of the project for the digital twin of the pump based on the expert judgement is 12 months, of which 6 months is the development of the hardware and software complex, and the remaining 6 months is the pilot operation (PO).
The total costs for the investment stage of the pilot project will amount to 21.83 mln RUR. Of these, it is necessary to allocate 13,920,000 RUR for design work, 5,000,000 RUR for software licensing, as well as 2,910,000 RUR – for hardware.
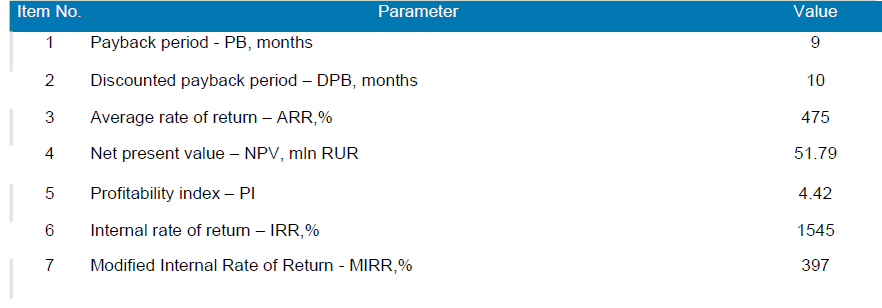
Let us estimate the expected economic effect from the implementation of the system by reducing the cost of maintenance of pumping equipment and preventing unplanned equipment downtime. Let us introduce the following assumptions and hypotheses:
– percentage of planned capacity losses: it is assumed that the refinery can sell the restored capacity; – the annual budget for maintenance of pumping equipment
– based on data from open purchases of leading Russian oil companies (Rosneft, Gazprom Neft, etc.);
– the annual budget for servicing pumping equipment does not consider capital repairs;
– avoidance of costs associated with more serious damage in relation to maintenance performed before the onset of equipment failure conditions;
– reducing the cost of unnecessary maintenance that is not required to ensure reliable operation (for example, preventive maintenance without identifying problems);
– reducing the cost of operations that caused damage due to cavitation, mechanical wear, etc.
– refinery marginality (profitability ratio per barrel) – based on the forecasts of the Big Four auditing companies. Let us assume that the refinery capacity is 10 mln t/year (i.e. 7.28 × 10 × 1,000,000/365 = 199,452 barrels of Urals grade oil per day). Let the profitability ratio per barrel be equal to 3 USD. Losses of the refinery’s production capacity associated with pumping equipment failures – 0.2%. Reduce production losses with remote process pump monitoring and predictive analytics – 30%. The estimated annual net profit growth is 199452 x 3 x 0.002 x 365 x 0.3 = 131,039 USD.
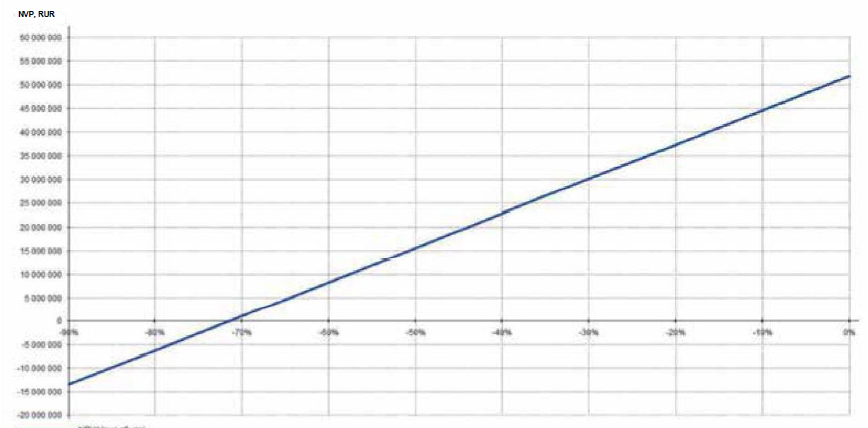
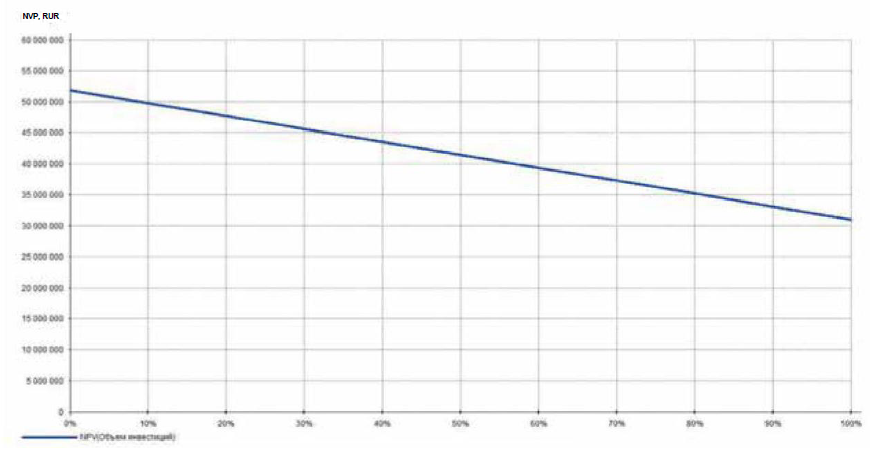
Let us estimate the expected economic effect from the implementation of the system by reducing the cost of maintenance of pumping equipment and preventing unplanned equipment downtime. Let us introduce the following assumptions and hypotheses:
– percentage of planned capacity losses: it is assumed that the refinery can sell the restored capacity; – the annual budget for maintenance of pumping equipment
– based on data from open purchases of leading Russian oil companies (Rosneft, Gazprom Neft, etc.);
– the annual budget for servicing pumping equipment does not consider capital repairs;
– avoidance of costs associated with more serious damage in relation to maintenance performed before the onset of equipment failure conditions;
– reducing the cost of unnecessary maintenance that is not required to ensure reliable operation (for example, preventive maintenance without identifying problems);
– reducing the cost of operations that caused damage due to cavitation, mechanical wear, etc.
– refinery marginality (profitability ratio per barrel) – based on the forecasts of the Big Four auditing companies. Let us assume that the refinery capacity is 10 mln t/year (i.e. 7.28 × 10 × 1,000,000/365 = 199,452 barrels of Urals grade oil per day). Let the profitability ratio per barrel be equal to 3 USD. Losses of the refinery’s production capacity associated with pumping equipment failures – 0.2%. Reduce production losses with remote process pump monitoring and predictive analytics – 30%. The estimated annual net profit growth is 199452 x 3 x 0.002 x 365 x 0.3 = 131,039 USD.
Let us estimate the decrease in annual costs for maintenance of pumping equipment. The annual budget for the maintenance of the refinery pumping equipment is 12 mln USD. Total annual cost of maintenance of refinery process pumps – 7%.
Reducing the average cost of repairs without unexpected pump failures – 30%. Thus, the reduction in annual maintenance costs would be 12,000,000 × 0.07 × 0.3 = 252 thousand USD. At the current rate of 75 RUR for 1 USD, it can be assumed that the total annual profit growth will amount to 28,727,925 RUR (or ~2.39 mln RUR/month).
The results of evaluating the effectiveness of investments in the project at a discount rate of 13.8% are presented in tab. 2.
The analysis of the sensitivity of the project to the sales price shows that the project of the hybrid digital twin of the pumping unit has more than 70% stock in terms of the sales price. If the volume of investments in the project doubles, the NPV of the project will amount to 30 mln RUR.
Conclusion
The digitalization trend of a large number of market segments is gaining momentum. The oil and gas industry, being a key industry for the Russian economy, did not remain aloof from this process.
Implementation of digital transformation is a complex and controversial task, in which it is necessary, first of all, to minimize the risks of an unplanned shutdown of the enterprise due to failures in the implementation of new technologies.
The pumping unit digital twin technology does not introduce changes in the technological structure that could lead to the shutdown of the refinery.
Analysis of international experience in such projects showed that the implementation of this technology at oil refineries allows to increase the efficiency of maintenance of dynamic equipment by 20-30%, reduce unplanned equipment downtime by 15-20%, reduce the volume of maintenance and repairs by 15-20% and reduce energy consumption per ton of oil by 2–5%. In Russia, work is also underway in this direction, but there are no real examples of industrial application, evaluation of the effectiveness and cost of such projects so far.
The economic effect from the introduction of a hybrid digital twin at a refinery with a capacity of 10 mln t/year of oil will be about 30 mln RUR/year by reducing the cost of maintenance of pumping equipment and preventing unplanned equipment downtime.
The total costs for the investment stage of the project, taking into account software and hardware and design work, are approximately 22 mln RUR Payback period of the project (PB) – 9 months, net present value (NPV) ~ 52 mln RUR.